4 內(nèi)齒圈齒廓的加工及測(cè)量
4.1內(nèi)齒圈齒廓的范成加工
目前,在推桿減速器的批量生產(chǎn)中,其內(nèi)齒圈齒廓的加工采用的都是范成加工方法,加工的夾具及刀具的相對(duì)運(yùn)動(dòng)完全模擬減速器的運(yùn)動(dòng)。激波器的偏心距e由一個(gè)偏心軸的偏心距e來(lái)實(shí)現(xiàn),激波器的半徑Tb與內(nèi)滾子半徑Tz之和由偏心軸的幾何中心至固定點(diǎn)的距離R來(lái)實(shí)現(xiàn),傳動(dòng)比由掛輪的傳動(dòng)比來(lái)實(shí)現(xiàn),如圖4.1所示。
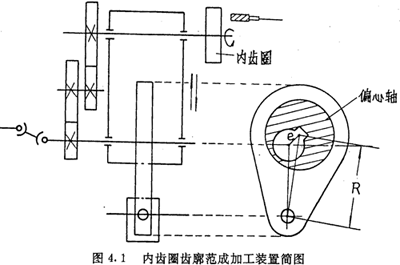
范成加工法具有快速、簡(jiǎn)易、經(jīng)濟(jì)的優(yōu)點(diǎn),其加式裝置可作為附件加裝在現(xiàn)有的滾齒機(jī)上。缺點(diǎn)是刀具必須完全與推桿外滾子直徑相同,而且對(duì)于推桿減速器的每一和中不同規(guī)格都要更換工裝,不利于產(chǎn)品系列化生產(chǎn)。盡管加工裝置本身可以調(diào)整得很精確,但常因刀具的磨損、進(jìn)刀深度掌握不當(dāng),以及刀具軸線沿內(nèi)齒圈徑向出現(xiàn)偏距等問(wèn)題給被加工的齒圈帶來(lái)很大誤差。
4.2內(nèi)齒圈齒廓的數(shù)控加工
內(nèi)齒圈齒廓可用數(shù)控銑進(jìn)行粗加工,用數(shù)控磨進(jìn)行精加工。本節(jié)主要討論在Y54非圓摟控插齒機(jī)上的加工方法。
4.2.1 Y54數(shù)控插齒機(jī)加工齒廓曲線的原理
經(jīng)Y54插齒機(jī)改造成的非圓數(shù)控加工機(jī)床,由X、C、D三軸聯(lián)動(dòng)來(lái)實(shí)現(xiàn)對(duì)給定曲線的數(shù)控加工,如圖4.2所示,D軸是刀具的回轉(zhuǎn)中心軸,加工齒廓曲線時(shí),采用圓形插刀,插刀一邊繞D軸旋轉(zhuǎn),一邊沿D軸作上下往復(fù)運(yùn)動(dòng)。C軸是工作臺(tái)回轉(zhuǎn)軸,被加工的工件加在工作臺(tái)上。沿X軸的移動(dòng)保證了沿齒深方向的進(jìn)刀量。X軸始終在刀具回轉(zhuǎn)中心D軸及工作臺(tái)回轉(zhuǎn)中心C軸的連線上。這三個(gè)軸分別由被脈沖信號(hào)驅(qū)動(dòng)的三個(gè)不同步進(jìn)電機(jī)所帶動(dòng)。根據(jù)被加工齒廓曲線的方程式,根據(jù)被加工齒廓曲線的方程式,可得出刀具中心軌跡方程,把它分解為沿X 軸方向的進(jìn)刀及繞工件C軸的旋轉(zhuǎn)兩個(gè)分量,即可實(shí)現(xiàn)對(duì)齒廓的數(shù)控加工。
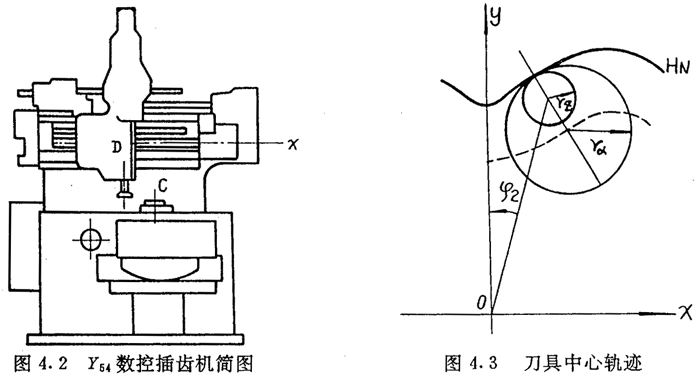
4.2.2刀具中心的軌跡
由上面可知,用數(shù)控加工齒廓時(shí),應(yīng)求出圓插刀中心的軌跡,它是被加工內(nèi)齒圈齒廓曲線的內(nèi)法向等距線,如圖4.3所示。圓插刀的半徑可不等于實(shí)際推桿減速器中滾子的半徑,只要刀具半徑Td小于內(nèi)齒圈齒廓在齒根部的最小曲率半徑,在加工過(guò)程中不會(huì)發(fā)生切削干涉即可。對(duì)于激波器為偏心圓的推桿減速器,根據(jù)(2.35)式,可得不發(fā)生切削干涉的條件為:
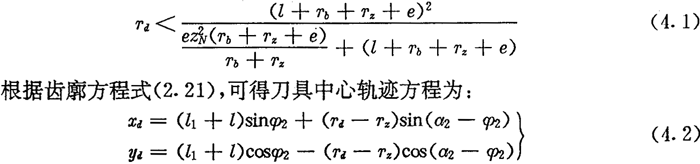
其中參數(shù)l1、a2與φ2關(guān)系為式(2.36)、(2.37)、(2.38)。
根據(jù)式(4.2)可算出數(shù)控插齒機(jī)所需的調(diào)整數(shù)據(jù)。
4.2.3數(shù)控編程
Y54數(shù)控插齒機(jī)的數(shù)控系統(tǒng)經(jīng)改進(jìn)后,可直接與普通微機(jī)進(jìn)行連接,通過(guò)微機(jī)上的一塊接口電路板直接控制步進(jìn)電機(jī)的驅(qū)動(dòng)電路。因而,數(shù)控驅(qū)動(dòng)程序可直接采用微機(jī)上的高級(jí)語(yǔ)言編制,其功能是將由刀具中心軌跡所得到的離散數(shù)據(jù),經(jīng)過(guò)一定的插補(bǔ)運(yùn)算,變?yōu)轵?qū)動(dòng)相應(yīng)步進(jìn)電機(jī)所需的脈沖數(shù)字信號(hào),從而完成要求的加工任務(wù)。
提供給數(shù)控驅(qū)動(dòng)程序的應(yīng)是一組分別向x軸、C軸、D軸發(fā)出的脈沖數(shù)nz、nc、nD,由數(shù)控驅(qū)動(dòng)程序?qū)@組脈沖進(jìn)行線性插補(bǔ)運(yùn)算,從而把輸入廓形信息轉(zhuǎn)化成步進(jìn)電機(jī)運(yùn)動(dòng)的脈沖串。其脈沖頻率由所要求的進(jìn)給速度決定。
線性插補(bǔ)采用數(shù)值積分法(DDA),其特點(diǎn)是運(yùn)行速度快,脈沖分配均勻,易于實(shí)現(xiàn)多軸運(yùn)動(dòng)及繪制各種函數(shù)曲線。具體實(shí)現(xiàn)方法是:
選擇位移量最大的軸為主導(dǎo)軸,即選取nz、nc、nD三個(gè)數(shù)中的最大值作為脈沖溢出基數(shù)nm,將nx、nc、nD分別向各自累加器中累加,每累加一次判斷各累加和是否大于溢出基值nm,若大于,則給該軸發(fā)一個(gè)脈沖,同時(shí)從該累加器中減去溢出基值nm,這樣主導(dǎo)軸每次迭代時(shí)必有一個(gè)脈沖輸出,其它兩軸只有在滿足條件時(shí)才有脈沖輸出,經(jīng)nm次迭代后,各軸同時(shí)達(dá)到終點(diǎn)(向各軸發(fā)完各自的脈沖數(shù))。
前面已求出加工內(nèi)齒圈齒廓時(shí)刀具中心的軌跡方程,為了得到數(shù)控驅(qū)動(dòng)程序所需的脈沖數(shù)據(jù),還應(yīng)將其曲線分成若干段,再求出每段中應(yīng)分別向三個(gè)軸所發(fā)的脈沖數(shù)。
為此,首先應(yīng)將式(4.2)化為極坐標(biāo)形式
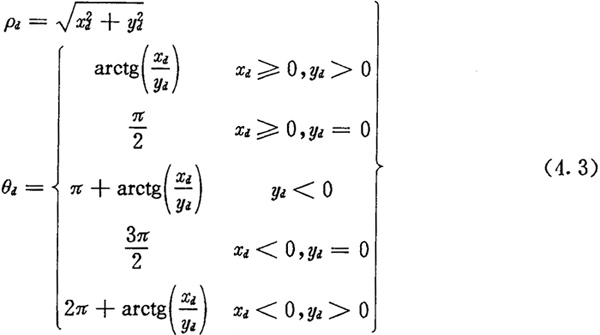
由于實(shí)際加工中是內(nèi)齒圈繞其身中心軸(工作臺(tái)C軸)旋轉(zhuǎn),而不是刀具繞C軸旋轉(zhuǎn),恨具只是沿x軸來(lái)回移動(dòng)。因而為形成式(4.3)所示的曲線,極徑ρd的變化由刀具沿x軸的變化來(lái)實(shí)現(xiàn),極角θd的變化由內(nèi)齒圈繞C軸的旋轉(zhuǎn)來(lái)實(shí)現(xiàn)。
在曲線上取若干點(diǎn),對(duì)相鄰兩點(diǎn)間的每一區(qū)段,極徑和極角都有相應(yīng)的增量△ρd及△θd,根據(jù)數(shù)控機(jī)床的技術(shù)參數(shù),可將△ρd及△θd轉(zhuǎn)換成相應(yīng)的脈沖數(shù)nx及nc。對(duì)于y54數(shù)控插齒機(jī),每個(gè)脈沖在x軸方向的進(jìn)給量是0.004mm,在C軸及D上轉(zhuǎn)動(dòng)的角度都是15″,因而:

上式中假定θd的單位是弧度。
D軸的轉(zhuǎn)動(dòng)只是為了使刀具磨損比較均勻,并不是形成內(nèi)齒圈齒廓所必須的運(yùn)動(dòng)。
具體編程時(shí)還應(yīng)注意脈沖的正負(fù)是否和所需的運(yùn)轉(zhuǎn)方向一致以及加工時(shí)刀具的初始位置。
4.2.4機(jī)床調(diào)整
機(jī)床調(diào)整的適當(dāng)與否,直接影響到被加工齒圈的質(zhì)量。加工內(nèi)齒圈齒廓時(shí)數(shù)控插齒機(jī)床的調(diào)整方法與在普通Y54插齒機(jī)上加工內(nèi)齒輪的調(diào)整方法大致相同。特別注意以下兩點(diǎn):
(1)內(nèi)齒圈齒坯的安裝與找正
內(nèi)齒圈齒廓的數(shù)控加工,是在齒圈外徑及兩端面都精加工后進(jìn)行的,因此,應(yīng)以端面及外徑作為定位基準(zhǔn)。其夾具可做成螺釘壓板結(jié)構(gòu),如圖4.4所示。夾具內(nèi)徑應(yīng)盡量接近齒圈外徑,用千分表以?shī)A具內(nèi)圓為基準(zhǔn)找正工作臺(tái)軸心。
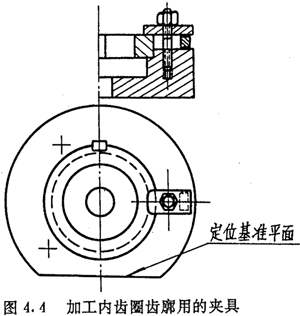
內(nèi)齒圈在推桿減速器的機(jī)座中是靠定位健來(lái)固定的。因而其外徑形有定位槽,裝配時(shí)兩個(gè)齒圈的定位槽應(yīng)分別位于機(jī)座的左右兩側(cè)。為了使同一推桿減速器中兩個(gè)齒廓形狀完全相同的內(nèi)齒圈能夠互成180°布置,在齒廓加工前,先在齒圈外徑上開(kāi)槽,數(shù)控加工以此鍵槽為刀具定位基準(zhǔn)。如圖4.4所示,為了便于找正,在制作夾具時(shí)相應(yīng)定位鍵槽制作一個(gè)定位基準(zhǔn)平面,通過(guò)千分表很容易使其與x軸平行。
(2)對(duì)刀
在數(shù)控加工過(guò)程中,刀具中心距(刀具中心離工件回轉(zhuǎn)中心的距離)反應(yīng)的就是由式(4.3)所表示曲線極徑,而在對(duì)刀時(shí),初始中心距與曲線初始極徑必須留有一定量的差距(一般為10mm~30mm),這段徑向差距留作數(shù)控加工一開(kāi)始由刀具徑向進(jìn)給來(lái)完成。因而所留差距量應(yīng)與數(shù)控程序中的相應(yīng)數(shù)據(jù)相符合。
徑向進(jìn)給量要掌握適當(dāng),不能太大。齒坯一般為圓環(huán)形,為了不致使進(jìn)給量過(guò)大,可分若干次進(jìn)行加工,每次都可使用同一個(gè)數(shù)據(jù)文件,只需在每次對(duì)刀時(shí),使刀具初始中心距作相應(yīng)的增加。
與范成法相比,數(shù)控加工的優(yōu)點(diǎn)是精度高,而且能做到使用同一把刀具加工不同規(guī)格的內(nèi)齒圈齒廓,并能對(duì)刀具磨損進(jìn)行補(bǔ)償。其缺點(diǎn)是對(duì)于進(jìn)行熱處理后的精加工必須使用數(shù)控磨床。
4.3內(nèi)齒圈齒廓的修形
4.3.1內(nèi)齒圈齒廓修形的目標(biāo)
由方程式(2.21)表示的內(nèi)齒圈齒廓是無(wú)側(cè)隙的,即圓周上所有的推桿,不論是否處于工作狀態(tài),都是和內(nèi)齒圈齒廓相接觸的。為了使推桿減速器便于裝拆和保證良好的潤(rùn)滑,實(shí)際的推桿減速器不能采用這種無(wú)隙嚙合的理論齒廓,而應(yīng)采用有隙嚙合的修形齒廓。修形齒廓就是有意識(shí)地將理論齒廓進(jìn)行微量修削后所得到的齒廓。對(duì)齒廓修形除了給嚙合傳動(dòng)留有一定量的間隙外,更重要的是使傳動(dòng)性能得到改善。所以修形齒廓的形狀和參數(shù)是內(nèi)齒圈齒廓加工的一個(gè)重要問(wèn)題。
內(nèi)齒圈齒廓修形后應(yīng)達(dá)到的理想狀態(tài)應(yīng)該是:第一,齒廓頂、根部修形量要以避免齒頂、齒根部參于嚙合,減小由于制造、裝配誤差造成的嚙合沖擊,提高嚙合效率。第二,在齒廓中部修形量要小且盡可能均勻分布,并有較長(zhǎng)的工作區(qū),以保證有足夠的同時(shí)嚙合齒數(shù),提高承載能力。第三,整個(gè)修形曲線要光滑,以保證機(jī)構(gòu)運(yùn)行平穩(wěn)。
4.3.2參數(shù)增量修形法
由內(nèi)齒圈的齒廓方程式可知,對(duì)內(nèi)齒圈齒廓有影響的參數(shù)是推桿長(zhǎng)度l,偏心圓激波器的半徑Tb,偏心距e以及滾子半徑Tz。在數(shù)控加工中,分別對(duì)每個(gè)參數(shù)給以不同的增量,則所形成的齒側(cè)間隙與范成加工中相應(yīng)工藝數(shù)增量引起的齒側(cè)間隙相同。因而單獨(dú)對(duì)某個(gè)參數(shù)給以增量或同時(shí)給幾個(gè)參數(shù)增量的不同組合,用計(jì)算機(jī)進(jìn)行大量的計(jì)算,得到各種不同形式的修形曲線及其規(guī)律,可供設(shè)計(jì)者選擇。
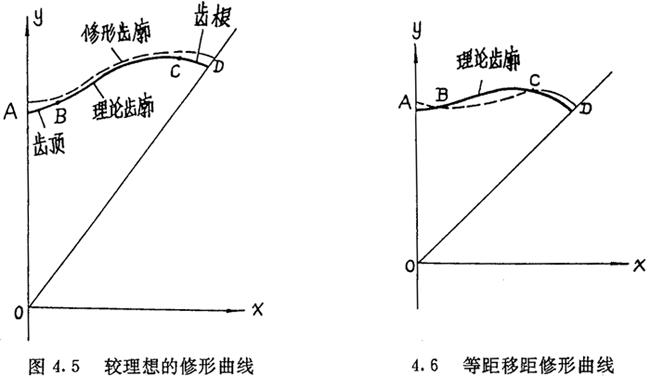
a.單一參數(shù)增量修形
等距修形:給參數(shù)Tz一個(gè)增量△Tz所得到的修形曲線是理論齒廓曲線的法向等距線。
移距修形:給參數(shù)l一個(gè)增量△1,或給參數(shù)Tb一個(gè)增量加△Tb,使被加工齒廓在原來(lái)理論情況下增加了一定量的進(jìn)刀深度。
單獨(dú)使用偏心增量助時(shí),會(huì)在齒頂段或齒根段產(chǎn)生過(guò)盈,故不宜采用。
可見(jiàn)單一參數(shù)增量法修形效果離前面提出的齒廓修形目標(biāo)相差太遠(yuǎn),故常采用它們的組合修形。
b.等距移距修形
給參數(shù)Tz一負(fù)值增量(-△Tz),同時(shí)給參數(shù)l一正值增量△l,計(jì)算表明修形曲線形狀如圖4.6中虛線所示。修形曲線實(shí)現(xiàn)了在齒頂,齒根修形量較大的目標(biāo)(圖4.6中的AB段及CD段),但要想在保持頂根修形量較大的前提下,在齒廓中段獲得較長(zhǎng)的工作區(qū)BC段,無(wú)論如何調(diào)整參數(shù)增量-△Tz及△l,都很難達(dá)到較理想的效果。對(duì)于其它組合修形,也有同樣的問(wèn)題。為此,需要研究一種更理想的修形方法。
4.3.3分段修形法
分段修形法是為了達(dá)到較理想的修形狀態(tài)而提出的一種能夠在數(shù)控加工中實(shí)現(xiàn)的齒廓修形方法。它根據(jù)修形后要達(dá)到的目標(biāo),將齒廓分成三段,如圖4.7所示,在工作段BC內(nèi)只進(jìn)行微量的等距修形,在齒頂段AB及齒根段CD內(nèi)同時(shí)進(jìn)行等距△Tz和移距△l增量函數(shù)修形。
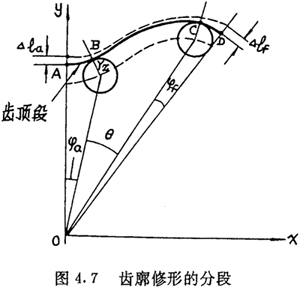
a.齒廓中段的修形
齒廓中段修形的要求是有較小且均勻分布的法向間隙。給參數(shù)Tz增量△Tz,可以達(dá)到這個(gè)目的。此時(shí)中段BC修形后的齒廓方程為:

上式中l(wèi)1、a2與φ2的關(guān)系仍為式(2.36)、(2.37)及(2.38),因?yàn)檫@些關(guān)系式中的Tz為內(nèi)滾子半徑,故不變。中段修形范圍是:
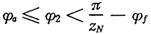
φa為齒頂修形角,φf為齒根修形角,見(jiàn)圖4.7。
b.齒頂段的修形
給定齒頂修形角φa,齒頂徑向最大修形量△la,選擇移距增量函數(shù)為:
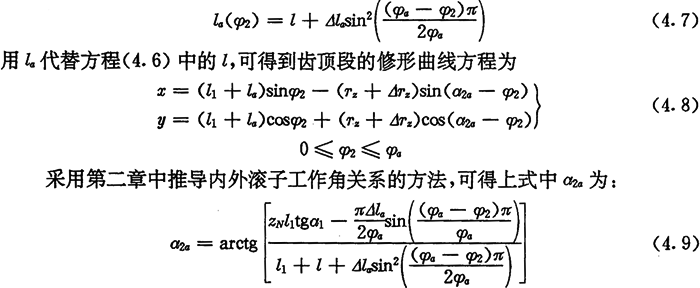
現(xiàn)在來(lái)證明齒頂修形曲線與中段修形曲線是光滑連接的。
第一,在φ2=φa處,兩曲線連續(xù)。顯然,當(dāng)φ2=φa時(shí),la=l,a2a=a2,此時(shí)方程(4.8)就變成了方程(4.6)。
第二,在φ2=φa處,兩曲線有相同的切線。設(shè)齒頂段修形曲線的切線斜率為ka,則由式(4.8)可得:

中段修形曲線的切線斜率km可由(4.6)式求得:

顯然在φ2=φa時(shí),有ka=km,即齒頂修形曲線與中段修形曲線光滑連接。
上一頁(yè)
下一頁(yè)