雙環(huán)減速器環(huán)板內(nèi)齒接觸分析及齒輪系統(tǒng)模態(tài)分析
3.1 雙環(huán)減速器環(huán)板內(nèi)齒接觸有限元分析
因為在少齒差內(nèi)嚙合中,不處于嚙合位置的齒對在進入嚙合之前以及在脫離嚙合之后,其內(nèi)、外齒廓間的間隙非常小,因此雙環(huán)減速器環(huán)板內(nèi)齒輪嚙合傳動在載荷作用下,因彈性變形實際接觸齒對數(shù)遠大于理論重合度,在傳遞載荷的過程中,輪齒的變形量要大于一部分齒對的間隙,這些齒對就要接觸并同時分擔載荷,這就大大提高了整個齒輪傳動裝置的承載能力。同時實際齒輪的接觸對數(shù)及接觸應力,隨著載荷增大而相應增加。因而少齒差內(nèi)嚙合行星齒輪傳動的實際接觸齒對數(shù)的確定,對齒輪承載能力的估算以及齒輪模數(shù)的正確確定具有重要意義。對于齒輪的接觸問題的,國內(nèi)外學者對此已作了不少研究,取得一些研究成果。然而這些研究有的沒有考慮誤差的影響,有的僅考慮內(nèi)外嚙合齒輪副齒廓理論間隙,沒有考慮輪齒制造誤差和輪齒的彈性變形的影響。本文對于環(huán)板內(nèi)齒輪接觸問題進行了計算,計算時考慮內(nèi)外嚙合齒輪副齒廓理論間隙、制造誤差及輪齒彈性變形的影響,在此基礎上,建立了少齒差內(nèi)嚙合行星齒輪傳動實際接觸齒對數(shù)及各齒間載荷分配的理論分析計算的實體模型,利用I-DEAS軟件進行了環(huán)板內(nèi)齒輪接觸有限元計算,并用該軟件分析計算了在不同載荷工況下的實際接觸齒對數(shù)、最大接觸應力以及兩環(huán)板上各接觸齒的載荷分配情況。
3.1.1 誤差對直齒內(nèi)嚙合傳動重合度的影響分析
通常,內(nèi)嚙合漸開線齒輪的理論計算是按無側隙的情況設計的,但要保證齒輪傳動靈活,不發(fā)生卡滯,必須保留足夠的齒側間隙,在實際制造與安裝中齒輪系統(tǒng)都必然存在尺寸誤差,這些誤差直接影響著齒輪傳動的精度、齒輪的強度和振動噪聲。
眾所周知,內(nèi)嚙合直齒圓柱齒輪傳動的理論重合度為:
設內(nèi)齒直齒輪傳動的齒輪模數(shù)為m,分度圓壓力角為a,外齒輪齒數(shù)為Z1,內(nèi)齒輪齒數(shù)為Z2,外、內(nèi)齒輪變位系數(shù)分別為X1、X2,外、內(nèi)齒輪變位系數(shù)分別為S1′、S2′,外、內(nèi)齒輪節(jié)圓上的齒槽寬分別為e1′、e2′,兩嚙合齒輪節(jié)圓上的圓周側隙為jt,兩嚙合齒輪非工作側齒廓沿公法線方向的側隙(法向側隙)為jn。顯然有

(3.2)
聯(lián)系式3.6與式3.8,從兩工中可以看出,計算中心距a′與嚙合角

′是一一對應關系,這樣式3.6可以表達為三種形式:
(1)由確定的齒側間隙jn與齒輪變位系數(shù)X2-X1來求中心距a′;
(2)由確定的中心距a′與齒輪變位系數(shù)X2-X1來求齒側間隙jn;
(3)由確定的齒側間隙jn與中心距a′來求齒輪變位系數(shù)X2-X1。
當齒輪傳動的幾何設計參數(shù)確定后,影響實際傳動的就只有制造和安裝誤差,對于中心距a′而言,影響它的因素是制造誤差、安裝誤差,而不是齒側間隙jn與齒輪變位系數(shù)X2-X1。齒輪設計是按無側隙進行的,同時不考慮制造、安裝誤差,但加工時,齒輪齒厚公差都是負偏差,即齒輪厚公差都是負偏差,即齒輪必須減薄,這樣實際傳動存在齒側隙。如果不考慮中心距的誤差,由式3.6的第3種形式可知,齒側隙的變化必然影響到齒輪變位系數(shù)的變化。顯然,這樣的變化也就會使齒輪的齒頂圓產(chǎn)生變化,相應的齒頂圓奢力角產(chǎn)生變化,進而影響齒輪嚙合重合度。
由式3.5變化為
本文實驗樣機的環(huán)板齒輪設計參數(shù)見表3.1所示,根據(jù)本文實驗樣機的環(huán)板齒輪設計參數(shù),假定嚙合角不變化,則對應齒側隙的變化,應用MATLAB繪圖分析,得到了齒輪變位系數(shù)隨齒側隙變化時的變化規(guī)律圖,見圖3.1所示。
表3.1 內(nèi)嚙合齒輪參數(shù)表
|
外齒輪 |
環(huán)板內(nèi)齒 |
模數(shù) |
2 |
齒數(shù) |
56 |
58 |
嚙合角 |
39.039° |
變位系數(shù) |
1.37 |
1.685 |
齒頂高系數(shù) |
0.7 |
中心距 |
2.42 |
齒頂圓直徑 |
119.519 |
120.774 |
計算重合度 |
1.124 |
由3.2圖可以看出,當齒側隙jn由0變化至.25毫米時(查資料取較大最小側隙參考值),齒輪變位系數(shù)差X2-X1的變化量由近0.32變化到0.50,變化了約0.18。
對于齒頂圓直徑按德國工業(yè)標準DIN的簡單方法有:

(3.10)(3.11)
由式3.10、3.11可以看出,當總變位系數(shù)

產(chǎn)生變化時,必然引起起嚙合齒輪齒頂圓直徑的變化。按X
1、X
2變化最小原則,有三種可能性,即X
1不變,X
2變化0~0.18;或X
1變化0~0.18,X
2不變;或X
1變小,X
2變大,變化范圍0~0.09。假定齒輪嚙合角不變,按本文實驗樣機參數(shù),當齒輪變位系數(shù)發(fā)生變化時,其變化量對重合度的影響狀況見圖3.2所示。從圖3.2所示可以看出,隨外齒輪變位變小時,齒輪嚙合重合度減小,隨內(nèi)齒輪變位變小時,齒輪嚙合重合度增大,從圖中的變化趨勢為看,外齒輪變位系數(shù)的變化對重合度的影響程度與內(nèi)齒輪變位系數(shù)的變化對重合度的影響程度大約是相同的,只是趨向是反向的。
對于中心距而言,查資料表35.2-60可知中心距的極限偏差為±0.011mm,假定外齒輪齒頂圓壓力角不變,內(nèi)齒輪齒頂圓壓力角隨變位系數(shù)變化,對于中心距變化對重合度的影響變化趨勢及變位系數(shù)變化對重合度的影響的變化趨勢比較情形見圖3.3。假定內(nèi)齒輪齒頂圓壓力角不變,外齒輪齒頂圓壓力角隨變位系數(shù)變化,對于中心距變化對重合度的影響變化趨勢及變位系數(shù)變化對重合度的影響的變化趨勢比較情形見圖3.4所示。
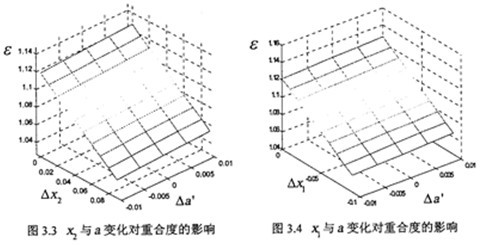
從圖3.3、3.4明顯看出中心距變化對重合度的影響程度明顯小于變位系數(shù)變化對重合度的影響程度。
齒輪制造誤差中對齒廓間隙影響較大的有最小齒側間隙、基節(jié)偏差、齒形誤差、齒距偏差、齒厚偏差等等,但這些因素相互關聯(lián)、相互制約、相互影響,特別是基節(jié)偏差、齒形誤差、齒距偏差、齒厚偏差等最終影響齒側隙的變化,因此最終影響齒輪傳動的主要因素仍是中心距和齒側隙的變化。分析圖3.2、3.3、3.4,在允許的制造誤差范圍內(nèi)及最小齒側隙的情況下,重合度的理論計算值變化不是很大。
3.1.2 接觸分析中制造安裝誤差的引入
從上述分析可知,齒輪的制造、安裝誤差對齒輪嚙合的重合度有一定的影響,但就理論計算值而言,從上面的分析結果可以看出其影響程度是不大的,然而在少齒差內(nèi)嚙合齒輪副中,嚙合線附近兩相鄰工作齒對齒側間隙非常小。假設內(nèi)齒輪固定,當輪齒承擔載荷時,兩接觸輪齒將分別產(chǎn)生彈性變形,外齒輪將繞其軸線旋轉一附加角,當這一附加轉角足夠大時,除原有接觸齒對繼續(xù)發(fā)生接觸外,相鄰工作齒對的齒側間隙也會消失,這樣就產(chǎn)生了多齒承載接觸。
在本節(jié)中,引入制造、安裝誤差,用有限元方法計算內(nèi)齒傳動的接觸對數(shù),同時驗證上節(jié)中討論的影響重合度的關鍵參數(shù)。用I-DEAS軟件計算環(huán)板內(nèi)齒接觸問題,其關鍵是齒輪輪齒的實體建模。對于相嚙合的齒輪,因其兩工作齒廓側面相互位置誤差的變化導致了實際齒廓間隙的變化,在嚙合線附近只有少數(shù)幾對齒在我們討論范圍內(nèi),這里我們只考慮對齒廓間隙影響較大的最小齒側間隙、基節(jié)偏差、齒形誤差、齒距偏差、齒厚偏差等。在用用I-DEAS軟件進行齒輪輪齒的實體建模時,對輪齒而言,沿圓周是均勻分布的,因此,齒輪的制造誤差在實體造型時,表現(xiàn)在齒輪輪齒的齒厚及基圓尺寸的誤差上。而經(jīng)多元回歸分析,得出各變量對齒廓間隙的內(nèi)在影響關系表明:齒輪的基節(jié)偏差是最主要的影響因素。
本文雙環(huán)減速器齒輪加工精度為7級,根據(jù)資料,查得齒輪的基節(jié)極限偏差△fpb為±0.014,對于齒厚極限偏差,根據(jù)資料,查得齒輪齒厚的極限偏差△Es的上偏差為-128μm,下偏差為-192μm,將這些影響因素的極限偏差,通過幾何關系的轉換,換算到基節(jié)上,通過參數(shù)方程繪出齒輪單個輪齒的輪廓線,再由單個輪齒的齒廓沿圓周接齒輪齒數(shù)均勻復制,這樣得到整個齒輪的齒廓線,由齒廓線延伸成齒輪實體模型。
由于零部件的制造誤差,同時因裝配原因,在進行整體裝配時,產(chǎn)生零部件間的安裝誤差,這些誤差直接影響齒輪間的嚙合狀態(tài)。對于雙環(huán)減速器中的環(huán)板內(nèi)齒輪嚙合傳動,由于環(huán)板內(nèi)齒中心與輸出齒輪中心之間的偏心距尺寸較。ū疚碾p環(huán)減速器的偏心距為2.42mm) ,因此,偏心軸的偏心距制造誤差及中心距制造安裝誤差是影響環(huán)板內(nèi)齒嚙合傳動的關鍵。本文雙環(huán)減速器兩偏心軸偏心距的制造誤差為±0.011 。
綜合以上誤差分析,將環(huán)板與輸出齒輪軸按極限偏差尺寸所定的位置進行輪齒嚙合裝配,然后進行有限元接觸分析。
3.1.3 齒輪有限元模型的建立及邊界條件的確定
環(huán)板內(nèi)齒輪與輸出軸齒輪之間的傳動是直齒輪傳動,為保證進行接觸計算時,有較多的有較接觸區(qū)域,齒輪輪齒部分的有限元網(wǎng)格采用映射網(wǎng)格劃分法(Mapped Meshing )對齒輪進行有限元網(wǎng)格劃分。同時,為保證兩對嚙合齒輪所劃分的網(wǎng)格接觸對相應的面能對應齊,因此齒輪嚙合的接觸面相應應當齊整。用輸出軸齒輪的齒頂面所在的輪廓曲面對環(huán)板內(nèi)齒進行劃分(partition 命令),同理用環(huán)板內(nèi)齒的齒頂面所在的輪廓曲面對輸出軸齒輪進行劃分,這樣得到對應齊整的齒輪嚙合的接觸面,如圖3.5所示。根據(jù)圖3.5所示,采用映射網(wǎng)格劃分法( Mapped Meshing)進行網(wǎng)格劃分的輪齒部分即是圖中輸出齒輪齒頂圓與環(huán)板內(nèi)齒齒頂圓之間所劃分的部分,而其余部分采用自由網(wǎng)格劃分法(Free Meshing)進行劃分,劃分網(wǎng)格后的部分網(wǎng)格圖見圖3.6所示?紤]實際接觸齒對數(shù)不會太多,所以每塊環(huán)板上只給出6個輪齒進行接觸計算。環(huán)板嚙合的實際過程是環(huán)板齒輪帶動輸出齒輪運動,計算時為方便,假設環(huán)板固定不動,設定輸出軸繞軸線轉動,將減速器的輸出功率換算為輸出扭矩,加在輸出軸的輸出端。

3.1.4 接觸計算結果分析
按考慮偏心距誤差影響及考慮齒厚誤差影響的兩個極限狀態(tài),組合為十種情況進行計算。十種計算工況見表3.2所示。考慮齒厚誤差影響的兩個極限狀態(tài)分別是齒輪的輪齒最薄、最厚,偏心距誤差的兩個極限狀態(tài)分別是偏心軸的偏心距最大、最小兩種情況。種接觸情況的計算結果分別由表3.3~3.7列出。
3.2計算工況列表
序
號 |
工況說明 |
序
號 |
工況說明 |
齒厚狀態(tài) |
偏心距狀態(tài) |
兩環(huán)板狀態(tài) |
齒厚狀態(tài) |
偏心距狀態(tài) |
兩環(huán)板狀態(tài) |
1 |
最厚 |
無誤差 |
對稱 |
6 |
最薄 |
最大正偏差 |
對稱 |
2 |
最薄 |
無誤差 |
對稱 |
7 |
最厚 |
最大負偏差 |
不對稱 |
3 |
最厚 |
最大負偏差 |
對稱 |
8 |
最薄 |
最大負偏差 |
不對稱 |
4 |
最薄 |
最大負偏差 |
對稱 |
9 |
最厚 |
最大正偏差 |
不對稱 |
5 |
最厚 |
最大負偏差 |
對稱 |
10 |
最薄 |
最大正偏差 |
不對稱 |
3.4工況一接觸情況計算表
誤差情況 |
載荷(N·m) |
接觸齒對數(shù) |
最大接觸應力(MPa) |
環(huán)板1
|
環(huán)板2 |
工
況
一 |
200 |
1 |
1 |
75.2 |
160 |
1 |
1 |
66.8 |
120 |
1 |
1 |
56.1 |
80 |
1 |
1 |
41.1 |
40 |
1 |
1 |
28.0 |
3.5工況二接觸情況計算表
誤差情況 |
載荷(N·m) |
接觸齒對數(shù) |
最大接觸應力(MPa) |
環(huán)板1
|
環(huán)板2 |
工
況
二 |
200 |
1 |
1 |
75.2 |
160 |
1 |
1 |
66.8 |
120 |
1 |
1 |
56.1 |
80 |
1 |
1 |
41.1 |
40 |
1 |
1 |
28.0 |
3.6工況三接觸情況計算表
誤差情況 |
載荷(N·m) |
接觸齒對數(shù) |
最大接觸應力(MPa) |
環(huán)板1
|
環(huán)板2 |
工
況
三 |
200 |
1 |
1 |
68.2 |
160 |
1 |
1 |
62.6 |
120 |
1 |
1 |
55.1 |
80 |
1 |
1 |
40.2 |
40 |
1 |
1 |
25.3 |
3.7工況四接觸情況計算表
誤差情況 |
載荷(N·m) |
接觸齒對數(shù) |
最大接觸應力(MPa) |
環(huán)板1
|
環(huán)板2 |
工
況
四 |
200 |
2 |
2 |
74.6 |
160 |
2 |
2 |
62.1 |
120 |
2 |
2 |
49.0 |
80 |
2 |
2 |
41.8 |
40 |
1 |
1 |
26.6 |
3.8工況五接觸情況計算表
誤差情況 |
載荷(N·m) |
接觸齒對數(shù) |
最大接觸應力(MPa) |
環(huán)板1
|
環(huán)板2 |
工
況
五 |
200 |
2 |
2 |
2.2 |
160 |
2 |
2 |
58.6 |
120 |
2 |
2 |
45.6 |
80 |
2 |
2 |
42.1 |
40 |
1 |
1 |
26.5 |
3.9工況六接觸情況計算表
誤差情況 |
載荷(N·m) |
接觸齒對數(shù) |
最大接觸應力(MPa) |
環(huán)板1
|
環(huán)板2 |
工
況
六 |
200 |
1 |
1 |
76 |
160 |
1 |
1 |
63.2 |
120 |
1 |
1 |
49.7 |
80 |
1 |
1 |
40.5 |
40 |
1 |
1 |
28.5 |
3.10工況七接觸情況計算表
誤差情況 |
載荷(N·m) |
接觸齒對數(shù) |
最大接觸應力(MPa) |
環(huán)板1
|
環(huán)板2 |
工
況
七 |
200 |
1 |
3 |
76 |
160 |
0 |
2 |
63.2 |
120 |
0 |
2 |
49.7 |
80 |
0 |
1 |
40.5 |
40 |
0 |
1 |
28.5 |
3.11工況八接觸情況計算表
誤差情況 |
載荷(N·m) |
接觸齒對數(shù) |
最大接觸應力(MPa) |
環(huán)板1
|
環(huán)板2 |
工
況
八 |
200 |
1 |
2 |
130.0 |
160 |
0 |
2 |
114.0 |
120 |
0 |
2 |
93.4 |
80 |
0 |
2 |
70.2 |
40 |
0 |
2 |
39.0 |
3.12工況九接觸情況計算表
誤差情況 |
載荷(N·m) |
接觸齒對數(shù) |
最大接觸應力(MPa) |
環(huán)板1
|
環(huán)板2 |
工
況
九 |
200 |
2 |
1 |
104.0 |
160 |
2 |
0 |
92.6 |
120 |
2 |
0 |
86.6 |
80 |
2 |
0 |
65.3 |
40 |
1 |
0 |
42.8 |
3.13工況十接觸情況計算表
誤差情況 |
載荷(N·m) |
接觸齒對數(shù) |
最大接觸應力(MPa) |
環(huán)板1
|
環(huán)板2 |
工
況
十 |
200 |
2 |
1 |
136.0 |
160 |
2 |
0 |
117. |
120 |
2 |
0 |
102.0 |
80 |
2 |
0 |
77.4 |
40 |
2 |
0 |
47.6 |
由表3.2~3.13可以看出,無論有無制造、安裝誤差的影響,隨著負荷的增加,齒輪實際嚙合接觸對數(shù)增加,但從計算結果分析證明,負荷對接觸對的影響小于誤差對接觸對的影響。對比表中的接觸對數(shù)和接觸應力,數(shù)據(jù)表明當齒厚發(fā)生變化時,實際接觸齒對數(shù)變化比較大,同時最大接觸應力也有明顯變化。從變化的趨勢上看出與前面的理論推導變化趨勢相同,這里只是更加明顯。
工況六至工況十這四和情況,是指兩環(huán)板之間不對稱,即偏心軸的兩個偏心拐的尺寸誤差不一致,這里考慮的是特殊狀況,從表3.10-3.13看出,當兩環(huán)板不對稱時,將產(chǎn)生嚴重的載荷不均現(xiàn)象,載荷偏向中心距小的環(huán)板內(nèi)齒上,甚至只有一個環(huán)板承受載荷。由此說明,對于雙環(huán)減速器偏心軸有加工,應特別注意兩曲捌的制造誤差,應盡量使安裝好的兩環(huán)板具有較好的對稱性。圖3.7~圖3.12為六種工況下環(huán)板內(nèi)齒的接觸齒對的應力云圖。
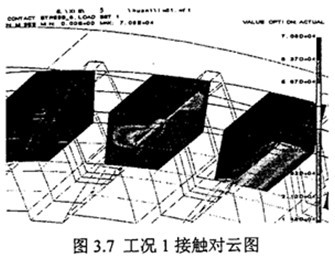

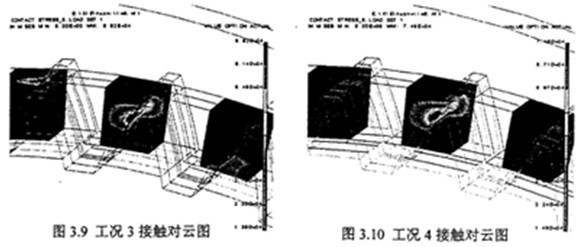

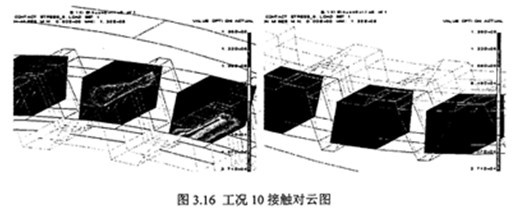
3.2 雙環(huán)減速器有限元模型建立及模態(tài)分析
近年來,隨著齒輪振動噪聲研究的不斷深入,不僅需要考慮齒輪系統(tǒng)及其嚙合過程,還必須考慮動態(tài)嚙合力在整個齒輪系統(tǒng)中的傳遞,以及系統(tǒng)中各零部件的固有特性和動態(tài)響應的性質(zhì),因此,必須以整個齒輪系統(tǒng)為研究對象,建立同時包括傳動系統(tǒng)和結構系統(tǒng)的完整系統(tǒng)的分析模型。本節(jié)將在雙環(huán)減速器運動特性分析的基礎上,以整個雙環(huán)減速器齒輪系統(tǒng)為對象,建立有限元動力分析模型,全面分析該系統(tǒng)的固有特性和動態(tài)響應。
齒輪系統(tǒng)的固有特性一般指系統(tǒng)的固有頻率和固有振型,是齒輪系統(tǒng)的動態(tài)特性之一,它對系統(tǒng)的動態(tài)響應,動載荷的產(chǎn)生與傳遞,以及系統(tǒng)振動的形式等都具有重要意義。此外,固有特性還是用振型疊加法求解系統(tǒng)響應的基礎。由于系統(tǒng)的固有特性表明了在哪些頻率下結構會產(chǎn)生共振以及在各階頻率下結構的相對變形,因此對于改善結構動態(tài)特性具有重要意義。通常,研究齒輪系統(tǒng)固有特性有理論計算法和實驗測試法兩種。實驗測試將在以后的章節(jié)中研究,本章將利用數(shù)值計算法計算雙環(huán)減速器齒輪系統(tǒng)的固有特性。結構系統(tǒng)固有特性的數(shù)值計算通常采用有限元模態(tài)分析方法。在有限元分析中,結構的動力學特征用微分方程組表征,則結構的固有頻率和固有振型相應地由動力學方程的特征值和特征向量所確定。所以可以說,求系統(tǒng)的固有頻率和固有振型即為求系統(tǒng)的特征值和特征向量。特征值問題的解法很多,主要有多項式割線迭代法、矢量逆迭代法、廣義雅可比法、子空間迭代法和行列式收縮法。動力問題有限元法是求解復雜結構的大型動力學方程組的特征值問題的有效方法。本章將用動力有限元法對雙環(huán)減速器齒輪系統(tǒng)進行特征值分析,計算其固有頻率和固有振型。
本文建立了齒輪系統(tǒng)的有限元動力學模型,用I-Deas 集成化軟件的固有模態(tài)求解模塊求解了齒輪系統(tǒng)的固有頻率和振型,并用響應動力(Response Dynamios ) 分析模塊研究了齒輪傳動系統(tǒng)的動態(tài)響應特性。要進行有限元模態(tài)分析,必須先建立齒輪系統(tǒng)的有限元力學模型。
3.2.1 齒輪系統(tǒng)有限元模型的建立
通常,實際工程結構都是質(zhì)量、剛度和阻尼連續(xù)分布的連續(xù)系統(tǒng),其動力學特性常常用偏微分方程組描述,但由于實際結構的幾何形狀及邊界條件復雜,難以用解析法求解偏微分方程組。于是,通常對實際工程結構離散化,將連續(xù)分布參數(shù)系統(tǒng)簡化為具有有限多個自由度的集中參數(shù)系統(tǒng)。用矩陣表達式對每個單元進行單元分析,根據(jù)虛位移原理建立單元的動態(tài)平衡方程式;然后,作整體分析,得到整個結構系統(tǒng)的動力學方程式。應用自由振動邊界條件,得到由有限元法計算整個結構系統(tǒng)固有振動特性的基本方程。這樣,通過離散化模型,可將復雜的偏微分方程組簡化為可以求解的常微分方程組,從而使問題的求解大大簡化。如前所述,雙環(huán)減速器結構運動特性復雜,既有旋轉齒輪運動,又有連桿平面運動,根據(jù)這一具體情況,本文用集中參數(shù)法建立了該傳動系統(tǒng)的彎——扭耦合振動的動力學分析模型。對箱體建立了有限元分析模型,該有限元模型的建立是用SDRC公司的I-Deas大型集成化軟件完成,并在此基礎上進行動力學響應分析計算。當進行系統(tǒng)的模態(tài)計算時,為了模型建立的方便,則將齒輪輪齒部分簡化為分度圓柱,將齒輪和輪毅及輪毅與軸的緊配合聯(lián)接看成剛性聯(lián)接,忽略鍵槽、倒角和退刀槽的影響,利用自由網(wǎng)格劃分法(Free Meshing)對齒輪進行有限元網(wǎng)格劃分。圖3.17為輸出齒輪軸的結構示意圖,齒輪的有關參數(shù)見表2.1。物理參數(shù)為:彈性模量E = 2.06×l011N/m2,泊松比為0.3, 材料密度p=7.8×103kg/m3。
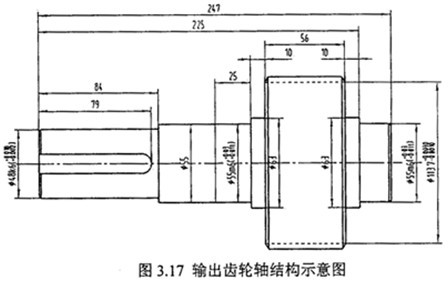
采用四節(jié)點四面體單元,利用軟件自由網(wǎng)格劃分法(Free Meshing )對輸出齒輪軸進行有限元網(wǎng)格劃分。減速箱的其它零件采用相同的方法進行有限元建模,圖3.18為輸出齒輪軸的有限元網(wǎng)格模型共劃分為3021個單元,835個節(jié)點,圖3.19為偏心軸的有限元網(wǎng)格模型,共劃分為4098個單元,1188個節(jié)點,圖3.20 為環(huán)板的有限元網(wǎng)格模型,共劃分為1505個單元,594個節(jié)點。
雙環(huán)減速器箱體是用鑄鐵鑄造而成,不考慮或?qū)Ψ治鲇绊懮跷⒌慕Y構特征,如小孔、園角、倒角、螺栓孔等,在進行減速箱實體建模時,忽略上述因素的影響,同時將箱蓋與箱體合為一體,而齒輪箱與前后端蓋、軸承組合而成,結構比較復雜,建模時不考慮頂蓋與箱體、前后端蓋、軸承與箱體的接合部的影響。軸承采用相同尺寸的圓環(huán)套,而其材料性質(zhì)用具有與軸承等效剛度相同的材料參數(shù),這些處理不會對齒輪箱體的重量及剛度產(chǎn)生大的影響,完全能保證足夠的計算精度。用自由網(wǎng)格劃分方法(Free Meshing),采用八節(jié)點四面體單元劃分網(wǎng)格,圖3.21為所建立的齒輪箱有限元模型網(wǎng)格,節(jié)點數(shù)為8761,單元數(shù)為28286。前面分別建立了齒輪系統(tǒng)主要零件和箱體的有限元網(wǎng)格,將簡化后的軸承用相同的方法進行有限元網(wǎng)格劃分,再用I-DEAS軟件的APPED命令將齒輪系統(tǒng)的各零部件集成為整個系統(tǒng)的有限元網(wǎng)格模型,如圖3.22 所示。
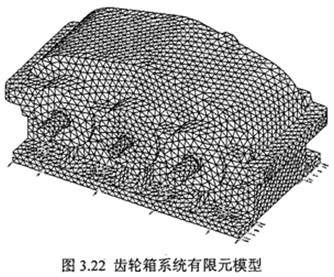
齒輪系統(tǒng)整個模型的單元數(shù)為112072,節(jié)點數(shù)為66120。
劃分有限元網(wǎng)格后,還必須對整個網(wǎng)格模型進行檢查,從而保證計算結果的真實性和準確性。首先檢查自由單元邊,當單元的某一邊不在其它單元之內(nèi)時,稱為自由單元邊。在復雜模型的建立過程中,通過拉伸旋轉等操作產(chǎn)生的各個部件,有時會沒有連接在一起,這將導致有限元模型開裂,影響計算結果,嚴重時將使計算失敗。其次檢查重復單元、重復節(jié)點,根據(jù)情況決定是否將它們合并在一起。最后檢查單元的形狀參數(shù),過度扭曲的單元將影響計算,必須并將其修改為可以接受的形狀。
3.2.2 齒輪系統(tǒng)有限元模態(tài)分析
結構模態(tài)是振動系統(tǒng)特性的一種表征。一般來說,模態(tài)參數(shù)包括固有頻率、固有振型、模態(tài)質(zhì)量、模態(tài)剛度和模態(tài)阻尼比等,但其中最重要的是前兩項。模態(tài)參數(shù)將表明在哪幾種頻率下結構會產(chǎn)生共振以及在各階頻率下結構的相對變形,對于改善結構的動態(tài)特性,這是最重要的基本參數(shù)。
通常,結構的前幾階固有頻率較低,對結構的動力學特性影響較大,所以分析時只提取齒輪系統(tǒng)結構的前20階固有頻率及其對應的振型便能滿足工程需要。為了能反映箱體的實際情況,在進行模態(tài)分析時將箱體底座z方向約束,地腳螺栓處用固定約束,研究系統(tǒng)的約束模態(tài)。利用I-DEAS軟件的固有模態(tài)求解模塊求解模型的固有頻率和固有振型的方法有:Lanczos法、Guyan Reduction法和同步向量迭代法(Simultaneous vecto: Iteraron,SVI)。Guyan法是決動力學問題的一種古典方法,但計算結果的精度在很大程度上取決于模型中的主自由度的選取。SVI法的精度不取決于用戶的判斷,但通常計算時間比Guyan法要長。一般求結構的固有頻率和固有振型時用Lanczos法,Lanczos法是近年來新興的一種模態(tài)求解方法,其特征值、特征向量求解精度高。它的計算速度比另兩種方法快,不需要選取“主自由度”,且要求的輸入數(shù)據(jù)較少。Lanczos法使用Stunn序列檢查,在用戶感興趣的頻率范圍內(nèi),在每個漂移點處如果不能找到所有的特征根,Lanczos法會給出提示信息,以避免漏根和引入不可能的根。用Lanczos法求解特征值和特征向量時,先根據(jù)載荷空間分布模式按一定規(guī)律生成一組相互正交的Lanezos向量,在將系統(tǒng)運動方程轉換到這組Lanczos向量空間以后,對運動方程進行縮減,然后通。過求解一次縮減了的運動方程的特征值問題,再經(jīng)過坐標系的變換,進而就可得到原系統(tǒng)的部分特征解,從而避免了一般算法如反迭代法或子空間迭代法中的多次迭代步驟,因而,顯著提高了求解效率。Lanczos方法適應面廣泛,可適用于所有的大中型結構問題,并都能給出很好的結果。
與其它特征值問題求解方法一樣,Lanczos算法的主要目的是求解結構系統(tǒng)的動力學方程。

(3.12)
式中M、C、K——系統(tǒng)的總質(zhì)量、阻尼和剛度矩陣

——系統(tǒng)節(jié)點加速度、速度和位移向量

——節(jié)點載荷向量
不考慮阻尼影響的多自由度系統(tǒng)自由振動方程為

(3.13)
設式(3.12)解的形式為

(3.14)
式中

——n階向量,位移向量

的幅值

——向量

振動的頻率
t0——由初始條件確定的時間常數(shù)
將式(3.14)代入式(3.13)得到特征方程為

(3.15)
或
KX=MXΩ2 (3.16)
式中,

,

,X、

分別為固有振型矩陣和固有頻率矩陣。
引入變換

(3.17)
式中,q(t)=[q1、q2 … qn]T,為廣義得位移向量,qi(i=1,2,…,n)為廣義位移值。
將上述變換代入式(3.12)中,兩端前乘XT,則式(3.12)成為n個解耦的二階常微分方程

(3.18)
式中

——模態(tài)阻尼因子

——無阻尼固有頻率

——模態(tài)力,

,是載荷向量

在振型{X}
i上的投影,若

按一定的空間分布模式而隨時間變化,即

(3.19)
上工中的符號s表示空間坐標。
則求解

(3.20)
正則化得,

,其中
再求解

(3.21)
將式(3.20)的解正交化得

(3.22)
式中,
為了保證和提供計算的穩(wěn)定性,需要對由式(3.22)計算得到的

進行重正交處理,即

(3.23)
式中,
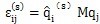
,上式中的

即為式(3.22)中的

,其迭計算終止于

滿足規(guī)定的誤差,或s達到某規(guī)定的值。然后將

恢復寫出為

,進行正則化計算得

,其中
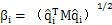
。
由式(3.21)、(3.22)和
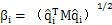
得到
(i=2,3,…,且q0=0)

(3.24)
式中,A=K-1M。將上式寫成矩陣形式為
AQ=QT (3.25)
式中,Q=[q1 q2 … qr],矩陣T如下式所示
(3.26)
引入原特征向量和Lanczos向量間的變換X
r=QZ(Z為r×r階矩陣),將原廣義特征值方程KX=MX

兩邊用Q
TMK
-1前乘、用

后乘得到用Lanczos向量內(nèi)三對角矩陣T表示的標準特征值問題,即

(3.27)
求解標準特征值問題式(3.27)的特征解:

(3.28)
由此計算得到原問題的部分特征解

(3.29)
從而使對A的特征值求解轉化為對T 的求解。由此可見,Lanczos算法的最大優(yōu)點是其所得的三對角陣T的特征解直接近似于原矩陣A中r個特征根。因此,對于僅需求解部分模態(tài)解的大型結構問題,Lanczos法可以在子空間內(nèi)非?焖儆行У厍蠼。本課題對系統(tǒng)各主要零部件及整體系統(tǒng)固有特性的求解就采用了這種方法。
如圖3.22 所示的齒輪系統(tǒng)有限元模型,根據(jù)實際的安裝情況,為了能比較準確地反映實際狀態(tài),箱體的邊界條件為:箱體底座垂直方向約束,四個螺栓孔處全部固定約束。則研究齒輪系統(tǒng)的約束模態(tài),表3.14~3.15分別為用I-Deas軟件的Lanczos模態(tài)求解法計算得到的各重要零部件及齒輪系統(tǒng)前上10階固有頻率和響應的振型情況。限于篇幅,圖3.23給出了齒輪系統(tǒng)的前十階固有振型。
表3.14 齒輪系統(tǒng)前10階固有頻率和振型
模型 |
固有頻率(Hz) |
振型特征 |
1 |
974.3714 |
箱體橫向(y向)彎曲 |
2 |
1219.1347 |
箱體橫向(x向)彎曲 |
3 |
1575.9162 |
輸入軸輸出軸彎曲+箱體扭擺 |
4 |
1690.4077 |
箱體底面向內(nèi)凹陷 |
5 |
1733.7038 |
輸入軸輸出軸向下彎曲 |
6 |
1738.6459 |
輸出軸輸出軸彎向上彎曲 |
7 |
1871.7482 |
輸入軸輸出軸水平彎曲 |
8 |
2345.6277 |
箱體兩邊膨脹中間向下凹陷 |
9 |
2657.8228 |
環(huán)板扭擺 |
10 |
2706.0426 |
輸入軸輸出軸彎曲向上彎曲+箱體扭彎 |
表3.15 零件前10階固有頻率
模態(tài) |
固有頻率(Hz) |
環(huán)板 |
輸出軸 |
偏心軸 |
輸入軸 |
箱體 |
1 |
1097.70 |
3004.30 |
2037.79 |
4538.75 |
890.79 |
2 |
1490.23 |
3021.40 |
2039.17 |
4542.69 |
1317.35 |
3 |
2355.64 |
6231.67 |
5118.85 |
10006.96 |
1428.24 |
4 |
2638.10 |
7985.83 |
5126.75 |
10326.25 |
1510.36 |
5 |
2977.05 |
8009.92 |
5590.44 |
10329.09 |
1681.76 |
6 |
3034.42 |
9210.48 |
8503.90 |
15266.32 |
1725.52 |
7 |
3457.06 |
13634.45 |
8939.29 |
18645.97 |
1761.74 |
8 |
3754.52 |
13704.50 |
8961.50 |
18668.88 |
2010.17 |
9 |
4296.74 |
14793.46 |
11425.93 |
19068.83 |
2021.84 |
10 |
4781.41 |
15484.25 |
13581.56 |
27836.97 |
2059.41 |
3.3 本章小結
在分析誤差對直齒內(nèi)嚙合傳動重合度的影響分析的基礎上,考慮部分制造誤差及安裝的影響,對環(huán)板內(nèi)齒的嚙合傳動,建立了考慮誤差的環(huán)板內(nèi)齒接觸有限元模型,并按不同的誤差狀態(tài),組合成十種不同的工況,對不同的工況分別建立了有限元接觸分析計算模型,通過計算結果分析討論了誤差及載荷變化的對齒輪接觸齒對的影響,指出了因載荷不均造成的減速器振動因素。
1)在雙環(huán)減速器齒輪系統(tǒng)的制造、安裝誤差中,齒輪側隙的誤差對齒輪重合度的影響大于中心距誤差對重合度的影響。而對于齒側隙的誤差大小重要是由于齒輪變位系數(shù)的變化造成的。即齒輪變位系數(shù)的誤差對齒輪重合度的影響大于中心距誤差對重合度的影響。
2)對于兩環(huán)板與輸出齒輪的傳動,如果兩環(huán)板對于輸出齒輪中心不對稱,即當兩偏心軸上的兩偏心曲拐的誤差不一致時,將產(chǎn)生兩環(huán)板嚴重的載荷不均現(xiàn)象。這是雙環(huán)減速器產(chǎn)生振動故障的重要因素。