內(nèi)齒圈齒廓的加工及測(cè)量
4.1內(nèi)齒圈齒廓的范成加工
目前,在推桿減速器的批量生產(chǎn)中,其內(nèi)齒圈齒廓的加工采用的都是范成加工方法,加工的夾具及刀具的相對(duì)運(yùn)動(dòng)完全模擬減速器的運(yùn)動(dòng)。激波器的偏心距e由一個(gè)偏心軸的偏心距e來實(shí)現(xiàn),激波器的半徑Tb與內(nèi)滾子半徑Tz之和由偏心軸的幾何中心至固定點(diǎn)的距離R來實(shí)現(xiàn),傳動(dòng)比由掛輪的傳動(dòng)比來實(shí)現(xiàn),如圖4.1所示。
范成加工法具有快速、簡(jiǎn)易、經(jīng)濟(jì)的優(yōu)點(diǎn),其加式裝置可作為附件加裝在現(xiàn)有的滾齒機(jī)上。缺點(diǎn)是刀具必須完全與推桿外滾子直徑相同,而且對(duì)于推桿減速器的每一和中不同規(guī)格都要更換工裝,不利于產(chǎn)品系列化生產(chǎn)。盡管加工裝置本身可以調(diào)整得很精確,但常因刀具的磨損、進(jìn)刀深度掌握不當(dāng),以及刀具軸線沿內(nèi)齒圈徑向出現(xiàn)偏距等問題給被加工的齒圈帶來很大誤差。
4.2內(nèi)齒圈齒廓的數(shù)控加工
內(nèi)齒圈齒廓可用數(shù)控銑進(jìn)行粗加工,用數(shù)控磨進(jìn)行精加工。本節(jié)主要討論在Y54非圓摟控插齒機(jī)上的加工方法。
4.2.1Y54數(shù)控插齒機(jī)加工齒廓曲線的原理
經(jīng)Y54插齒機(jī)改造成的非圓數(shù)控加工機(jī)床,由X、C、D三軸聯(lián)動(dòng)來實(shí)現(xiàn)對(duì)給定曲線的數(shù)控加工,如圖4.2所示,D軸是刀具的回轉(zhuǎn)中心軸,加工齒廓曲線時(shí),采用圓形插刀,插刀一邊繞D軸旋轉(zhuǎn),一邊沿D軸作上下往復(fù)運(yùn)動(dòng)。C 軸是工作臺(tái)回轉(zhuǎn)軸,被加工的工件加在工作臺(tái)上。沿X 軸的移動(dòng)保證了沿齒深方向的進(jìn)刀量。X軸始終在刀具回轉(zhuǎn)中心D軸及工作臺(tái)回轉(zhuǎn)中心C軸的連線上。這三個(gè)軸分別由被脈沖信號(hào)驅(qū)動(dòng)的三個(gè)不同步進(jìn)電機(jī)所帶動(dòng)。根據(jù)被加工齒廓曲線的方程式,根據(jù)被加工齒廓曲線的方程式,可得出刀具中心軌跡方程,把它分解為沿X 軸方向的進(jìn)刀及繞工件C軸的旋轉(zhuǎn)兩個(gè)分量,即可實(shí)現(xiàn)對(duì)齒廓的數(shù)控加工。
4.2.2刀具中心的軌跡
由上面可知,用數(shù)控加工齒廓時(shí),應(yīng)求出圓插刀中心的軌跡,它是被加工內(nèi)齒圈齒廓曲線的內(nèi)法向等距線,如圖4.3所示。圓插刀的半徑可不等于實(shí)際推桿減速器中滾子的半徑,只要刀具半徑Td小于內(nèi)齒圈齒廓在齒根部的最小曲率半徑,在加工過程中不會(huì)發(fā)生切削干涉即可。對(duì)于激波器為偏心圓的推桿減速器,根據(jù)(2. 35)式,可得不發(fā)生切削干涉的條件為:
其中參數(shù)l
1、a
2與

關(guān)系為式(2.36)、(2.37)、(2.38)。
根據(jù)式(4.2)可算出數(shù)控插齒機(jī)所需的調(diào)整數(shù)據(jù)。
4.2.3數(shù)控編程
Y54數(shù)控插齒機(jī)的數(shù)控系統(tǒng)經(jīng)改進(jìn)后,可直接與普通微機(jī)進(jìn)行連接,通過微機(jī)上的一塊接口電路板直接控制步進(jìn)電機(jī)的驅(qū)動(dòng)電路。因而,數(shù)控驅(qū)動(dòng)程序可直接采用微機(jī)上的高級(jí)語言編制,其功能是將由刀具中心軌跡所得到的離散數(shù)據(jù),經(jīng)過一定的插補(bǔ)運(yùn)算,變?yōu)轵?qū)動(dòng)相應(yīng)步進(jìn)電機(jī)所需的脈沖數(shù)字信號(hào),從而完成要求的加工任務(wù)。
提供給數(shù)控驅(qū)動(dòng)程序的應(yīng)是一組分別向x軸、C軸、D軸發(fā)出的脈沖數(shù)nz、nc、nD,由數(shù)控驅(qū)動(dòng)程序?qū)@組脈沖進(jìn)行線性插補(bǔ)運(yùn)算,從而把輸入廓形信息轉(zhuǎn)化成步進(jìn)電機(jī)運(yùn)動(dòng)的脈沖串。其脈沖頻率由所要求的進(jìn)給速度決定。
線性插補(bǔ)采用數(shù)值積分法(DDA),其特點(diǎn)是運(yùn)行速度快,脈沖分配均勻,易于實(shí)現(xiàn)多軸運(yùn)動(dòng)及繪制各種函數(shù)曲線。具體實(shí)現(xiàn)方法是:
選擇位移量最大的軸為主導(dǎo)軸,即選取nz、nc、nD三個(gè)數(shù)中的最大值作為脈沖溢出基數(shù)nm,將nx、nc、nD分別向各自累加器中累加,每累加一次判斷各累加和是否大于溢出基值nm,若大于,則給該軸發(fā)一個(gè)脈沖,同時(shí)從該累加器中減去溢出基值nm,這樣主導(dǎo)軸每次迭代時(shí)必有一個(gè)脈沖輸出,其它兩軸只有在滿足條件時(shí)才有脈沖輸出,經(jīng)nm次迭代后,各軸同時(shí)達(dá)到終點(diǎn)(向各軸發(fā)完各自的脈沖數(shù))。
前面已求出加工內(nèi)齒圈齒廓時(shí)刀具中心的軌跡方程,為了得到數(shù)控驅(qū)動(dòng)程序所需的脈沖數(shù)據(jù),還應(yīng)將其曲線分成若干段,再求出每段中應(yīng)分別向三個(gè)軸所發(fā)的脈沖數(shù)。
為此,首先應(yīng)將式(4.2)化為極坐標(biāo)形式
由于實(shí)際加工中是內(nèi)齒圈繞其身中心軸(工作臺(tái)C軸)旋轉(zhuǎn),而不是刀具繞C軸旋轉(zhuǎn),恨具只是沿x軸來回移動(dòng)。因而為形成式(4.3)所示的曲線,極徑Pd的變化由刀具沿x軸的變化來實(shí)現(xiàn),極角θd的變化由內(nèi)齒圈繞C軸的旋轉(zhuǎn)來實(shí)現(xiàn)。
在曲線上取若干點(diǎn),對(duì)相鄰兩點(diǎn)間的每一區(qū)段,極徑和極角都有相應(yīng)的增量△Pd及△θd轉(zhuǎn)換成相應(yīng)的脈沖數(shù)nx及nc。對(duì)于y54數(shù)控插齒機(jī),每個(gè)脈沖在x軸方向的進(jìn)給量是0.004mm,在C軸及D上轉(zhuǎn)動(dòng)的角度都是15",因而:
上式中假定θd的單位是弧度。
D軸的轉(zhuǎn)動(dòng)只是為了使刀具磨損比較均勻,并不是形成內(nèi)齒圈齒廓所必須的運(yùn)動(dòng)。
具體編程時(shí)還應(yīng)注意脈沖的正負(fù)是否和所需的運(yùn)轉(zhuǎn)方向一致以及加工時(shí)刀具的初始位置。
4.2.4機(jī)床調(diào)整
機(jī)床調(diào)整的適當(dāng)與否,直接影響到被加工齒圈的質(zhì)量。加工內(nèi)齒圈齒廓時(shí)數(shù)控插齒機(jī)床的調(diào)整方法與在普通Y54插齒機(jī)上加工內(nèi)齒輪的調(diào)整方法大致相同。特別注意以下兩點(diǎn):
(1)內(nèi)齒圈齒坯的安裝與找正
內(nèi)齒圈齒廓的數(shù)控加工,是在齒圈外徑及兩端面都精加工后進(jìn)行的,因此,應(yīng)以端面及外徑作為定位基準(zhǔn)。其夾具可做成螺釘壓板結(jié)構(gòu),如圖4.4所示。夾具內(nèi)徑應(yīng)盡量接近齒圈外徑,用千分表以夾具內(nèi)圓為基準(zhǔn)找正工作臺(tái)軸心。
內(nèi)齒圈在推桿減速器的機(jī)座中是靠定位健來固定的。因而其外徑形有定位槽,裝配時(shí)兩個(gè)齒圈的定位槽應(yīng)分別位于機(jī)座的左右兩側(cè)。為了使同一推桿減速器中兩個(gè)齒廓形狀完全相同的內(nèi)齒圈能夠互成180°布置,在齒廓加工前,先在齒圈外徑上開槽,數(shù)控加工以此鍵槽為刀具定位基準(zhǔn)。如圖4.4所示,為了便于找正,在制作夾具時(shí)相應(yīng)定位鍵槽制作一個(gè)定位基準(zhǔn)平面,通過千分表很容易使其與x軸平行。
(2)對(duì)刀
在數(shù)控加工過程中,刀具中心距(刀具中心離工件回轉(zhuǎn)中心的距離)反應(yīng)的就是由式(4.3)所表示曲線極徑,而在對(duì)刀時(shí),初始中心距與曲線初始極徑必須留有一定量的差距(一般為10mm~30mm),這段徑向差距留作數(shù)控加工一開始由刀具徑向進(jìn)給來完成。因而所留差距量應(yīng)與數(shù)控程序中的相應(yīng)數(shù)據(jù)相符合。
徑向進(jìn)給量要掌握適當(dāng),不能太大。齒坯一般為圓環(huán)形,為了不致使進(jìn)給量過大,可分若干次進(jìn)行加工,每次都可使用同一個(gè)數(shù)據(jù)文件,只需在每次對(duì)刀時(shí),使刀具初始中心距作相應(yīng)的增加。
與范成法相比,數(shù)控加工的優(yōu)點(diǎn)是精度高,而且能做到使用同一把刀具加工不同規(guī)格的內(nèi)齒圈齒廓,并能對(duì)刀具磨損進(jìn)行補(bǔ)償。其缺點(diǎn)是對(duì)于進(jìn)行熱處理后的精加工必須使用數(shù)控磨床。
4.3內(nèi)齒圈齒廓的修形
4.3.1內(nèi)齒圈齒廓修形的目標(biāo)
由方程式(2.21)表示的內(nèi)齒圈齒廓是無側(cè)隙的,即圓周上所有的推桿,不論是否處于工作狀態(tài),都是和內(nèi)齒圈齒廓相接觸的。為了使推桿減速器便于裝拆和保證良好的潤(rùn)滑,實(shí)際的推桿減速器不能采用這種無隙嚙合的理論齒廓,而應(yīng)采用有隙嚙合的修形齒廓。修形齒廓就是有意識(shí)地將理論齒廓進(jìn)行微量修削后所得到的齒廓。對(duì)齒廓修形除了給嚙合傳動(dòng)留有一定量的間隙外,更重要的是使傳動(dòng)性能得到改善。所以修形齒廓的形狀和參數(shù)是內(nèi)齒圈齒廓加工的一個(gè)重要問題。
內(nèi)齒圈齒廓修形后應(yīng)達(dá)到的理想狀態(tài)應(yīng)該是:第一,齒廓頂、根部修形量要以避免齒頂、齒根部參于嚙合,減小由于制造、裝配誤差造成的嚙合沖擊,提高嚙合效率。第二,在齒廓中部修形量要小且盡可能均勻分布,并有較長(zhǎng)的工作區(qū),以保證有足夠的同時(shí)嚙合齒數(shù),提高承載能力。第三,整個(gè)修形曲線要光滑,以保證機(jī)構(gòu)運(yùn)行平穩(wěn)。
4.3.2參數(shù)增量修形法
由內(nèi)齒圈的齒廓方程式可知,對(duì)內(nèi)齒圈齒廓有影響的參數(shù)是推桿長(zhǎng)度l,偏心圓激波器的半徑Tb,偏心距e以及滾子半徑TZ0在數(shù)控加工中,分別對(duì)每個(gè)參數(shù)給以不同的增量,則所形成的齒側(cè)間隙與范成加工中相應(yīng)工藝數(shù)增量引起的齒側(cè)間隙相同。因而單獨(dú)對(duì)某個(gè)參數(shù)給以增量或同時(shí)給幾個(gè)參數(shù)增量的不同組合,用計(jì)算機(jī)進(jìn)行大量的計(jì)算,得到各種不同形式的修形曲線及其規(guī)律,可供設(shè)計(jì)者選擇。
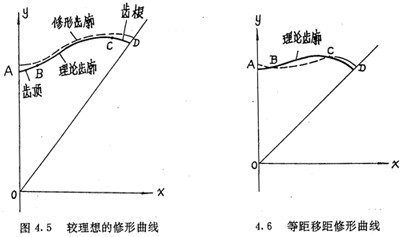
a.單一參數(shù)增量修形
等距修形:給參數(shù)T
Z一個(gè)增量△T
Z所得到的修形曲線是理論齒廓曲線的法向等距線。
移距修形:給參數(shù)l一個(gè)增量△1,或給參數(shù)T
b一個(gè)增量加△T
b,使被加工齒廓在原來理論情況下增加了一定量的進(jìn)刀深度。
單獨(dú)使用偏心增量助時(shí),會(huì)在齒頂段或齒根段產(chǎn)生過盈,故不宜采用。
可見單一參數(shù)增量法修形效果離前面提出的齒廓修形目標(biāo)相差太遠(yuǎn),故常采用它們的組合修形。
b.等距移距修形
給參數(shù)Tz一負(fù)值增量(-△Tz),同時(shí)給參數(shù)l-正值增量△l,計(jì)算表明修形曲線形狀如圖4.6中虛線所示。修形曲線實(shí)現(xiàn)了在齒頂,齒根修形量較大的目標(biāo)(圖4.6中的AB段及CD段),但要想在保持頂根修形量較大的前提下,在齒廓中段獲得較長(zhǎng)的工作區(qū)BC段,無論如何調(diào)整參數(shù)增量-△Tz及△l,都很難達(dá)到較理想的效果。對(duì)于其它組合修形,也有同樣的問題。為此,需要研究一種更理想的修形方法。
4.3.3分段修形法
分段修形法是為了達(dá)到較理想的修形狀態(tài)而提出的一種能夠在數(shù)控加工中實(shí)現(xiàn)的齒廓修形方法。它根據(jù)修形后要達(dá)到的目標(biāo),將齒廓分成三段,如圖4.7所示,在工作段BC內(nèi)只進(jìn)行微量的等距修形,在齒頂段AB及齒根段CD內(nèi)同時(shí)進(jìn)行等距△Tz和移距△l增量函數(shù)修形。
a.齒廓中段的修形
齒廓中段修形的要求是有較小且均勻分布的法向間隙。給參數(shù)Tz增量△Tz,可以達(dá)到這個(gè)目的。此時(shí)中段BC修形后的齒廓方程為:
上式中l(wèi)
1、a
2與

的關(guān)系仍為式(2.36)、(2.37)及(2.38),因?yàn)檫@些關(guān)系式中的T
Z為內(nèi)滾子半徑,故不變。中段修形范圍是:
現(xiàn)在來證明齒頂修形曲線與中段修形曲線是光滑連接的。
第一,在

=

處,兩曲線連續(xù)。顯然,當(dāng)

=

時(shí),l
a=l,a
2a=a
2,此時(shí)方程(4.8)就變成了方程(4.6)。
第二,在

=

處,兩曲線有相同的切線。設(shè)齒頂段修形曲線的切線斜率為k
a,則由式(4.8)可得:
中段修形曲線的切線斜率km可由(4.6)式求得:
顯然在

=

時(shí),有k
a=k
m,即齒頂修形曲線與中段修形曲線光滑連接。
c.齒根段的修形
給定齒根修形角

和徑向最大修形量△l
f,選擇移距增量函數(shù):
同樣可以證明,齒根修形曲線與中段修形曲線也是光滑連接的。
4.3.4修形對(duì)工作推桿數(shù)的影響
內(nèi)齒圈齒廓修形之后,由于工作區(qū)域角的減小,使同時(shí)參加工作的推桿數(shù)也會(huì)有所減少。相鄰兩推桿之間的中心角為

,而一個(gè)齒所對(duì)應(yīng)的中心角為

,

與

之差體現(xiàn)了相鄰兩個(gè)推桿相對(duì)所在齒廓初始位置的差異,記△

=

-

,稱△

為位置差角,如圖4.8所示。從圖可知,工作推桿的數(shù)目等于推桿工作區(qū)域角與△

的比值。推桿工作區(qū)域角指推桿從嚙合傳力開始到結(jié)束時(shí)推動(dòng)傳動(dòng)圈轉(zhuǎn)過的角度。在不修形的理論情況下,推桿工作區(qū)域角是

,經(jīng)修形后,頂根段不參與嚙合,工作區(qū)域角為“θ=

,所以實(shí)際工作推桿數(shù)n
g為:
顯然,未經(jīng)修形的齒廓曲線在齒頂鄰域和齒根鄰域嚙合的壓力角都很小,因而分段修形后應(yīng)將頂、根部大致削去相同的區(qū)段。即
、

仰的分配應(yīng)根據(jù)各自所對(duì)應(yīng)的頂根段曲線弧長(zhǎng)相等的原則來進(jìn)行。一般可近似取

為

的2到4倍,而取△l
f=esin

。
[計(jì)算實(shí)例]:
對(duì)于TW-3-16推桿減速器,要求內(nèi)齒圈齒廓經(jīng)修形后同時(shí)工作的推桿數(shù)ng不少于5,按上述方法確定的修形量為:
取

,則

=3°,

,△l
a=0.36mm選擇△T
Z=0.19mm,將齒廓分段修形后,機(jī)器性能得到了明顯改善。
4.4內(nèi)齒圈齒廓的公法線測(cè)量及加工精度控制
目前在推桿減速器的大批量生產(chǎn)中,對(duì)內(nèi)齒圈齒廓的加工所采用的還都是范成加工方法,其測(cè)量手段長(zhǎng)期以來一直沒能得到很好的解決。一些生產(chǎn)廠家主要是利用測(cè)量齒根至齒圈外圓的厚度及齒頂至齒圈外圓的厚度來確定被加工齒廓的合格與否。這種方法并沒有能夠完全反應(yīng)出內(nèi)齒圈齒廓在加工過程中所產(chǎn)生的誤差,它僅斃反應(yīng)出偏心距的誤差。公法線測(cè)量法是以預(yù)先計(jì)算出的公法線理論長(zhǎng)度為依據(jù),根據(jù)測(cè)量的結(jié)果,能夠判斷出加工過程中影響內(nèi)齒圈齒廓加工精度的各個(gè)控制參數(shù)所產(chǎn)生的誤差,從而對(duì)這些參數(shù)進(jìn)行調(diào)整,使之達(dá)到要求的精度。
4.4.1公法線的長(zhǎng)度計(jì)算
如圖4.9 所示,AB是其中一個(gè)齒槽的一側(cè)齒廓,A′B′是跨槽數(shù)為K(圖中k=4)的一個(gè)齒梢的另一側(cè)齒廓,它們是兩個(gè)性質(zhì)不同的齒廓。若把AB看成是工作齒廓,則A′B′是非工作齒廓。選擇圖4.9所示的坐標(biāo)系,讓坐標(biāo)原點(diǎn)O與內(nèi)齒圈幾何中心重合,y軸與OA重合。設(shè)P(x,y)為AB齒廓上的一點(diǎn),在P點(diǎn)與內(nèi)齒圈齒廓相接觸的外滾子的位置角為

,在A′B′上取P點(diǎn)的對(duì)應(yīng)點(diǎn)P′,使∠A′OO
2=

,P′點(diǎn)與P點(diǎn)是關(guān)于∠AOA′的平分線完全對(duì)稱的,即0P′=OP,a
2=

,OO
1=00
2,圖4.9中PO
1與P′O
2相交在Q點(diǎn),它們并不共線,因此P′點(diǎn)與P點(diǎn)不具有共同的法線。假設(shè)隨著P點(diǎn)位置的改變(當(dāng)然P′點(diǎn)也隨著P的改變而改變),使PO
1與P′O
2在同一條直線上,此時(shí)P′與P就有共同的法線,此時(shí):
上式就是齒廓AB上與跨槽數(shù)為k的齒廓具有公法線的點(diǎn)的條件。當(dāng)k確定后,若存在公法線,則由(4.17)式并結(jié)合基本關(guān)系式(2.38)等可解出

的值來。
從圖4.9可求得公法線長(zhǎng)度為:
Wk=2(l1+l)cosa2+2rz (4.18)
式中l(wèi)
1、a
2與

的關(guān)系由基本關(guān)系式所確定。顯然,兩個(gè)齒槽的同側(cè)齒廓(同為工作齒廓或非工作齒廓)是不存在公法線的。
4.4.2公法線的數(shù)目
由于內(nèi)齒圈齒廓曲線具有周期性且工作齒廓與非工作齒廓是完全對(duì)稱的,所以只需討論一個(gè)齒槽的一側(cè)齒廓與其它齒槽的另一側(cè)齒廓所具有的公法線。
令:
內(nèi)齒圈的齒數(shù)Z
N可以是奇數(shù),也可以是偶數(shù)(實(shí)際產(chǎn)品都是奇數(shù))。為了討論問題的方便,引用截?cái)嗳≌?hào)“INT”,當(dāng)Z
N為偶數(shù)時(shí),INT

等于

,當(dāng)Z
N為奇數(shù)時(shí),INT

等于

,由函數(shù)式(4.19)可得:
下面就來講議化跨槽數(shù)k取不同數(shù)值時(shí),具有的公法線情況:
(1)跨槽數(shù)k≤INT

的情況
由(4.12)式及(4.22)式知,若Z
N為奇當(dāng)選,有f(0)<0,f

<0;若Z
N為偶數(shù),有f(0)<0,f

<0,因而不論Z
N是奇數(shù)還是偶數(shù),方程(4.20)在區(qū)間[0,

]內(nèi)若有解,則必為兩個(gè)。為找出函數(shù)f(

)在區(qū)間[0,

]內(nèi)的極大點(diǎn),令
由上式結(jié)合基本關(guān)系式,利用計(jì)算機(jī)可解出

在區(qū)間[0,

]內(nèi)f(

)的極大點(diǎn)。顯然,若極大值為正,則公法線有兩條,若極大值為負(fù),則公法線不存在。分析計(jì)算還表明,在極大點(diǎn)前,函數(shù)f(

)單調(diào)增加,在極大點(diǎn)后,函數(shù)f(

)單調(diào)減小。一般極大點(diǎn)接近

,為討論方便,選

=

作特征點(diǎn),代替極大點(diǎn)討論,經(jīng)計(jì)算證實(shí),不會(huì)影響解的正確性。假若f(

) >0,則在[0,

]內(nèi)必有兩個(gè)點(diǎn)滿足方程(4.20),這兩個(gè)點(diǎn)對(duì)應(yīng)的

值分別位于[0,

],(

,

之內(nèi)。結(jié)合圖4.9可知,位于[0,

]內(nèi)的點(diǎn),其公線是凸齒公線,而位于(

,

公法線凹齒公線。凸齒公線是被測(cè)兩個(gè)齒廓上最短的連線,凹齒公法線是被測(cè)兩個(gè)齒廓上最長(zhǎng)的連線。這使得實(shí)際測(cè)量成為可行。假若f(

)<0,則公法線不存在。
則當(dāng)跨槽數(shù)k<k
0時(shí),兩齒廓不存在公法線。當(dāng)INT

≥k>k
0時(shí),兩齒廓具有凸凹兩條公法線。
故方程(4.20)只在區(qū)間(

,

內(nèi)有解,即兩齒廓只有一條凹齒公法線。
當(dāng)Z
N為偶數(shù)時(shí),有f(0)>0,

,故兩齒廓也只有一條凹齒公法線,且位于

=

把跨槽數(shù)k取到k
0到INT(

) +1之間不同整數(shù)值時(shí)所具有的公法線合在一起就是內(nèi)齒圈齒廓所具有的各種不同長(zhǎng)度的公法線總數(shù)。
[算例]
對(duì)于前面提到的3TWY7.5-12推桿減速器,齒數(shù)ZN=11,計(jì)算得到k0=4,即當(dāng)跨槽數(shù)k小于等于4時(shí),兩齒郭不具有公法線。當(dāng)跨槽數(shù)k=5時(shí),計(jì)算得到兩條公法線,理論長(zhǎng)度分別為:
凸齒公法線 W
51=209.632mm,對(duì)應(yīng)于

=1.755°
凹齒公法線 W
52=215.716mm,對(duì)應(yīng)于

=12.485°
當(dāng)跨槽數(shù)k=6時(shí),計(jì)算得出只有 條凹齒公法線
W
63=230.146mm,對(duì)應(yīng)于

=15.205°
合起來,此推桿減速器的內(nèi)齒圈齒廓共有三條不同長(zhǎng)度的公法線,它們的位置如圖4.10所示。
4.4.3刀具軸線有偏距時(shí)的內(nèi)齒廓及公法線
用圓柱形刀具加工內(nèi)齒圈齒廓時(shí),刀具軸線應(yīng)在齒圈的半徑方向作相對(duì)運(yùn)動(dòng),如果它不沿著齒圈半徑方向運(yùn)動(dòng),那就有了偏距。在圖4.11中,若刀具中心的運(yùn)動(dòng)方向平行于y軸,而刀具中心在O2處,那就有了偏距E,現(xiàn)在來分析此時(shí)加工出來的齒廓及公法線長(zhǎng)度,
同圖4.11可得:
利用第二章中推導(dǎo)內(nèi)外滾子工作角關(guān)系的方法可得a2與a1的關(guān)系為:
經(jīng)過分析可知,當(dāng)存在偏距E時(shí),在跨槽數(shù)為k的兩齒廓上具有公法線的點(diǎn)的條件仍然可用式(4.17)表示,公法線長(zhǎng)度為:
若令(4.30)式和(4.31)式中的E=0,得到的就是無偏距時(shí)的內(nèi)齒圈齒廓理論方程式(2.21)及公法線長(zhǎng)度(4.18)式。
4.4.4利用公法線誤差分析加工調(diào)整參數(shù)誤差
由齒廓方程式(4.30)可以知道,齒廓形狀取決于偏心軸的偏心距e,偏心軸幾何中心到固定點(diǎn)長(zhǎng)度R,刀具半徑TZ,進(jìn)刀深度l以及刀具軸線偏距E。e和R是夾具結(jié)構(gòu)上的固定尺寸,應(yīng)該調(diào)整得盡量正確,而其誤差加△e、△R也是個(gè)定值。而△TZ是由于刀具制造誤差及加工過程中的磨損引起,△l及△E是由于操作誤差引起。因此,△TZ、△l及△E是導(dǎo)致齒形誤差的工藝因素。下面來分析它們對(duì)公法線長(zhǎng)度的影響。
把公法線長(zhǎng)度Wk看成是自變量為TZ、l及E的函數(shù),即Wk=Wk(TZ,l,E),由(4.31)式可得:
假設(shè)用下標(biāo)i表示公法線序號(hào),用△Wki表示第i條公法線實(shí)際測(cè)量出的值與理論計(jì)算出的值的誤差,則可得到公法線長(zhǎng)度誤差方程為:
則:
上式中A-1是矩陣A的逆陣,稱誤差矩陣。當(dāng)算得相應(yīng)的偏導(dǎo)數(shù)值后,如果測(cè)得一個(gè)齒槽的一側(cè)齒廓與其它齒廓的三條公法線的誤差,代入方程組(4.32)之后,便可求得相應(yīng)的△TZ、△l和△E!鱐Z是經(jīng)計(jì)算得到的刀具半徑的誤差,△l是進(jìn)刀深度誤差,△E是刀具軸線偏心距的誤差,根據(jù)計(jì)算結(jié)果適當(dāng)調(diào)整這些參數(shù)就能迅速地提高齒廓精度,使之達(dá)到精度要求。
[計(jì)算實(shí)例〕
前面所說的3TWT7.5-12推桿減速器,根據(jù)參數(shù)可計(jì)算得到其誤差矩陣A-1為:
在一個(gè)內(nèi)齒圈齒廓上實(shí)際測(cè)得三條公法線的長(zhǎng)度與理論長(zhǎng)度的誤差為:
△W51=0.02261mm
△W52=0.03806mm
△W63=0.02106mm
代入式(4.32)可得:
△TZ=0.0202mm,△l=0.032mm,△E=0.1697mm
根據(jù)計(jì)算結(jié)果適當(dāng)調(diào)整這些參數(shù)就能迅速提高齒廓精度,使之達(dá)到精度要求。