韌性減速機(jī)理與相關(guān)數(shù)值模擬
上一章討論了穩(wěn)態(tài)擴(kuò)展前提下的輸氣管道動(dòng)態(tài)斷裂有限元計(jì)算。之所以很多研究把穩(wěn)態(tài)擴(kuò)展作為前提,并曾在相當(dāng)長(zhǎng)的時(shí)間內(nèi)采用Kalininen估算管道極限裂紋擴(kuò)展速度的(2-6a)式計(jì)算裂紋穩(wěn)態(tài)擴(kuò)展速度,是因?yàn)楦邏狠斔团d起以來,人們?cè)L(zhǎng)期認(rèn)為材料的抗力遠(yuǎn)遠(yuǎn)不足以抵御高壓氣體逸出引起的裂紋驅(qū)動(dòng)力,裂紋不斷被加速驅(qū)動(dòng),直至擴(kuò)展速度達(dá)到了接近于極限速度的穩(wěn)態(tài)值。這確實(shí)符合早期動(dòng)態(tài)脆性斷裂的觀測(cè)結(jié)果。
隨著冶金技術(shù)水平的提高,管材的性能發(fā)生了較大的變化。與此同時(shí),管線的設(shè)計(jì)壓力也有了大的提高。原有的動(dòng)態(tài)脆性斷裂幾乎不再發(fā)生。新的動(dòng)態(tài)延性斷裂乃至高壓高韌性斷裂能夠?qū)е聰嗔阉俣冉咏跇O限,并形成穩(wěn)態(tài)擴(kuò)展嗎?這個(gè)穩(wěn)態(tài)擴(kuò)展的前提值得懷疑。
3.1從韌性變化看鋼制管道動(dòng)態(tài)斷裂
在天然氣管線裂紋止裂研究的歷史上,對(duì)管線斷裂現(xiàn)象認(rèn)識(shí)有一個(gè)提高的過程。在管線建設(shè)的早期,由于當(dāng)時(shí)冶金水平的局限,管材的韌性水平較低,韌脆轉(zhuǎn)化溫度DBTT(Ductile-to-Brittle Transition Temperature)較高,發(fā)生了很多管線的脆性斷裂事故。防止脆性斷裂的發(fā)生是人們的主要研究課題。管線的工作溫度在管線鋼的DBTT以下時(shí),動(dòng)態(tài)斷裂呈現(xiàn)宏觀脆性斷裂的特征,即其橫縱向斷口都為平直的只有很少剪切唇或完全沒有剪切唇的脆性斷口。這種動(dòng)態(tài)脆性斷裂(DBF)沿著管道的對(duì)稱面發(fā)展,如圖3-1a所示。
為了防止管線脆性斷裂事故的發(fā)生,人們進(jìn)行了大量的研究工作,提出了用管材的夏比沖擊韌性值和落錘撕裂實(shí)驗(yàn)(DWTT)的斷口形貌轉(zhuǎn)化溫度作為判定管線是否發(fā)生脆性斷裂的依據(jù)。
此后鋪設(shè)的管線采用了DBTT低于管線工作溫度的鋼材,用高壓多次加壓檢測(cè)可能會(huì)產(chǎn)生的缺陷,改進(jìn)老管線的操作條件等多種措施。實(shí)踐表明,這些措施較為可靠,基本解決了動(dòng)態(tài)脆性斷裂的問題。
20世紀(jì)70年代以來,隨著純凈鋼、連鑄板坯及低碳微合金化鋼板控軋技術(shù)的發(fā)展,管材的韌性得到飛躍性的提高。隨后又引入了計(jì)算機(jī)自動(dòng)控制技術(shù)和多探頭的無損探傷技術(shù)等,能夠保證超高壓運(yùn)行的高韌性管道得以實(shí)現(xiàn)。近年來,超純凈鋼的出現(xiàn)為直焊縫管的發(fā)展提供了原材料方面更大的支持,加上整體熱處理、熱張力減徑等原用于無縫管軋制的技術(shù)引用于直焊縫管生產(chǎn),其產(chǎn)品向高等級(jí)、多元化方向發(fā)展,其性能己等同或超過無縫管。
在管道用鋼韌性性能大幅度上升的背景下,20世紀(jì)60年代,延性失穩(wěn)斷裂事故首次在輸氣管線上出現(xiàn)。動(dòng)態(tài)延性斷裂(DDF)在宏觀剪切面上擴(kuò)展,與管道表面呈45度傾斜角,有很大的剪切唇,如圖3-lb和圖3-1c所示。雖然這種斷裂的環(huán)境溫度高于鋼材的韌脆轉(zhuǎn)化溫度,但由于鋼材的韌性相對(duì)于強(qiáng)度較低,還是使動(dòng)態(tài)斷裂擴(kuò)展先于顯著的塑性應(yīng)變而發(fā)生。
圖3-2顯示了DBF和DDF的形貌特征。從圖中看出動(dòng)態(tài)延性斷裂相比于脆性斷裂具有速度較低,裂紋擴(kuò)展途徑比較單一,能自行止裂等特點(diǎn)。由于脆性斷裂已被廣泛遏止,近二十年來,人們把注意力主要集中在延性斷裂的起裂擴(kuò)展和止裂上,對(duì)延性斷裂的關(guān)注遠(yuǎn)超過對(duì)脆性斷裂的研究,目前還遠(yuǎn)未結(jié)束。管線鋼動(dòng)態(tài)斷裂韌性的測(cè)定也就成為了人們關(guān)注的焦點(diǎn)。
3.2全尺寸實(shí)驗(yàn)中出現(xiàn)的減速現(xiàn)象
為了清楚地闡述在國(guó)外高韌性輸氣鋼管的全尺寸爆破實(shí)驗(yàn)中觀測(cè)到的由材料韌性引起的裂紋持續(xù)減速現(xiàn)象,有必要先對(duì)全尺寸實(shí)驗(yàn)的方法作較為細(xì)致的描述。本節(jié)的數(shù)據(jù)還會(huì)用作第四章小試樣實(shí)驗(yàn)和本章的韌性減速計(jì)算的比較。
說到全尺寸實(shí)驗(yàn),就不能不提憑借全尺寸實(shí)驗(yàn)數(shù)據(jù)進(jìn)行止裂預(yù)測(cè)的Maxey雙曲線法。下面我們就從Maxey雙曲線法開始對(duì)全尺寸實(shí)驗(yàn)中得到的結(jié)果以及遇到的問題做歸納性的陳述,同時(shí)引出本文的發(fā)現(xiàn)和觀點(diǎn)。
3.2.1Maxey雙曲線方法
在延性斷裂的止裂研究中,人們一直試圖確定材料的韌性值達(dá)到多大,可以使管線具有足夠的止裂能力。由于全尺寸實(shí)驗(yàn)相當(dāng)昂貴,且結(jié)果僅對(duì)應(yīng)于特定的天然氣成分、管道性能等因素,因此需要對(duì)實(shí)驗(yàn)的特性進(jìn)行定量化以用于動(dòng)態(tài)延性斷裂止裂設(shè)計(jì)。關(guān)于止裂韌性臨界值的預(yù)判模型,國(guó)際上應(yīng)用較多的是1975年BMI的Maxey等人建立的雙曲線(Two-Curve)方法。
雙曲線法的具體分析過程如圖3-3所示,坐標(biāo)橫軸表示速度,縱軸表示氣體壓力或環(huán)向應(yīng)力。上方的一組曲線表征不同韌性水平下的斷裂速度,是內(nèi)壓或環(huán)向應(yīng)力的函數(shù)。隨著內(nèi)壓或環(huán)向應(yīng)力在斷裂過程中的減小,斷裂速度不斷降低。如果壓力或應(yīng)力足夠低,斷裂速度即減小到零而發(fā)生止裂。
下面的虛線與氣體減壓波速有關(guān),它也是環(huán)向應(yīng)力或管道內(nèi)壓的函數(shù)。在減壓過程中,連續(xù)的減壓波沿管子傳播,對(duì)應(yīng)于每個(gè)壓力有一個(gè)唯一的波擴(kuò)展速度。因此在減壓波沿管線從開裂源傳播時(shí)在很寬的速度范圍內(nèi)壓力是連續(xù)的。
根據(jù)管道動(dòng)態(tài)斷裂擴(kuò)展與止裂的減壓波速判據(jù),當(dāng)裂紋擴(kuò)展速度低于管內(nèi)介質(zhì)的減壓波速度時(shí),裂紋會(huì)停止擴(kuò)展;當(dāng)裂紋擴(kuò)展速度高于管內(nèi)介質(zhì)的減壓波速時(shí),不會(huì)發(fā)生止裂。
這種說法的依據(jù)是:對(duì)于前一種情況,從裂源處開始,減壓波前沿的移動(dòng)速度比斷裂擴(kuò)展速度更快,使得裂紋尖端的管壁應(yīng)力因減壓波的通過而不斷減小,并最終降至止裂應(yīng)力水平以下而使裂紋止裂;反之裂紋尖端的壓力不發(fā)生變化,斷裂將持續(xù)擴(kuò)展,因?yàn)榱鸭y尖端的動(dòng)態(tài)襲紋驅(qū)動(dòng)力不會(huì)減小。
如果斷裂速度曲線和壓力波速曲線不相交,則在任何條件下減壓波速都大于斷裂速度。根據(jù)減壓波速判據(jù),裂紋擴(kuò)展將發(fā)生止裂。如果兩曲線相交或相切,則最少有一點(diǎn)壓力所對(duì)應(yīng)的壓力波速和斷裂速度是相等的。這時(shí)管道將發(fā)生持續(xù)的裂紋擴(kuò)展。因此,圖3-3中兩條曲線的切點(diǎn)對(duì)應(yīng)于止裂所需的臨界韌性,切點(diǎn)處的橫坐標(biāo)即為穩(wěn)態(tài)擴(kuò)展情況下的斷裂速度。
為了得到數(shù)值解答,Maxey的延性斷裂模型總結(jié)出了裂紋擴(kuò)展速度和管內(nèi)壓力(或環(huán)向應(yīng)力)之間的經(jīng)驗(yàn)關(guān)系:
式中vf表示斷裂擴(kuò)展速度(m/s);C是由經(jīng)驗(yàn)確定的回填常數(shù);σf為流動(dòng)應(yīng)力,MPa,σf =(σy+σu)/2,σy為屈服應(yīng)力,σu為拉伸強(qiáng)度:c2/3為2/3厚度試樣的夏比沖擊韌性值(J/mm2);Pd為裂尖處的氣體壓力(MPa);Pa為止裂時(shí)的氣體壓力(MPa);σH為裂尖處的環(huán)向應(yīng)力(MPa);σa為止裂時(shí)的環(huán)向應(yīng)力(MPa)。
式(3-l)中止裂壓力(環(huán)向應(yīng)力)Pa(σa)有如下的計(jì)算關(guān)系式:
式中R為管道半徑(mm);E為彈性模量(MPa);h為管道壁厚(mm)。
這種雙曲線法的處理還被用于處理富氣輸送問題。乙烷等其它烷類氣體的混入引起了兩相減壓行為。在兩相狀態(tài)下,減壓波速曲線會(huì)在相變過程區(qū)產(chǎn)生平臺(tái),表明相變阻礙了氣體從開裂的管道中逸出,使得裂紋止裂更加困難。
在雙曲線法的基礎(chǔ)上,結(jié)合大量的實(shí)驗(yàn)結(jié)果對(duì)止裂韌性進(jìn)行標(biāo)定,世界各大研究機(jī)構(gòu)分別給出了簡(jiǎn)便易算的經(jīng)驗(yàn)公式用以估算臨界止裂韌性,列舉如下:
其中c2/3為估算的2/3尺寸單位面積夏比沖擊臨界止裂韌性(J/mm2);d為埋入深度(mm);其余符號(hào)的物理意義與單位與前面相同。
Maxey雙曲線法及導(dǎo)出的經(jīng)驗(yàn)公式的優(yōu)點(diǎn)在于理論及算法比較簡(jiǎn)單,易于工程應(yīng)用,因而從20世紀(jì)70年代起被國(guó)際上廣泛采納,并通過了實(shí)驗(yàn)的檢驗(yàn)。
必須指出的是,這些經(jīng)驗(yàn)公式都是根據(jù)早期的低韌性全尺寸實(shí)驗(yàn)(CVN能量小于100J)數(shù)據(jù)經(jīng)常數(shù)標(biāo)定而得出的,對(duì)于高韌性管線鋼,這些公式出現(xiàn)了明顯的偏差。隨著近年來管道鋼管材料特性的變化,材料強(qiáng)度及韌性的提高,以及高壓富氣輸送工藝的采用使已有的止裂預(yù)測(cè)公式偏于危險(xiǎn)。
圖3-4表示了Battelle應(yīng)用Maxey雙曲線法對(duì)全尺寸實(shí)驗(yàn)數(shù)據(jù)庫所做的DDF止裂韌性預(yù)測(cè),圖3-4a至圖3-4f分別對(duì)應(yīng)于式(3-3)至式(3-8)。圖中顯示的實(shí)驗(yàn)用管的鋼級(jí)包括X52到Xl00,管徑范圍從4O6mm到1422mm,實(shí)驗(yàn)最高壓力超過16MPa?梢,預(yù)測(cè)模型在管材韌性低于某一水平時(shí)預(yù)測(cè)結(jié)果與實(shí)物實(shí)驗(yàn)結(jié)果基本吻合,但當(dāng)管材韌性較高時(shí)出現(xiàn)明顯偏差,預(yù)測(cè)應(yīng)該止裂的管線沒有止裂。經(jīng)典的止裂預(yù)測(cè)模型在預(yù)測(cè)夏比能量值高于94J的管材時(shí),已經(jīng)偏于危險(xiǎn),即過高估計(jì)了管材的止裂性能。
為了保留原有的經(jīng)驗(yàn)算法,1997年Leis認(rèn)為保證該算法準(zhǔn)確的臨界韌性值為94J,并對(duì)高韌性結(jié)果做了修正:
預(yù)測(cè)沖擊韌性CVN>94J時(shí):CVN′=CVN+O.002CCVN2.04-21.18 (3-9)
預(yù)測(cè)止裂沖擊韌性CVN<-94J時(shí)因非線性影響不明顯而不做修正。
這種修正方法僅是一定范圍內(nèi)根據(jù)真實(shí)實(shí)驗(yàn)結(jié)果的近似歸納,并不能從趨勢(shì)上解決雙曲線法在描述高韌性淬火回火鋼時(shí)出現(xiàn)的偏差。其原因是高韌性鋼出現(xiàn)后,傳統(tǒng)的動(dòng)態(tài)實(shí)驗(yàn)手段引起與斷裂無關(guān)的顯著能量散失。
3.2.2全尺寸爆破實(shí)驗(yàn)(Full-Scale Burst Test)簡(jiǎn)介
全尺寸實(shí)驗(yàn)的費(fèi)用昂貴,周期長(zhǎng)。實(shí)驗(yàn)過程中要求系統(tǒng)地變化壓力、管徑、壁厚、強(qiáng)度以及韌性等變量,因此實(shí)驗(yàn)操作難度大,重復(fù)次數(shù)多。國(guó)內(nèi)做過水壓爆破實(shí)驗(yàn),高壓輸氣管道實(shí)驗(yàn)尚無先例。目前已知的實(shí)驗(yàn)數(shù)據(jù)來源有意大利CSM的鋼制管道實(shí)驗(yàn)、美國(guó)西南研究院的PE管道實(shí)驗(yàn)、加拿大一美國(guó)聯(lián)盟管道實(shí)驗(yàn)和日本HLP組織實(shí)驗(yàn)。
全尺寸爆破實(shí)驗(yàn)一般設(shè)有一根有預(yù)制裂紋的低韌性鋼管在管段中部作為起裂管,兩側(cè)焊接鋼管的韌性沿裂紋擴(kuò)展方向遞增排列。裂紋從起裂管向兩側(cè)擴(kuò)展,停止擴(kuò)展部位的鋼管韌性就是設(shè)定運(yùn)行條件下的管線止裂所需的韌性。斷裂擴(kuò)展速率在低韌性的起裂管開裂后測(cè)量。
全尺寸實(shí)驗(yàn)使用甲烷、空氣或者氦氣作為壓力介質(zhì)。實(shí)驗(yàn)分為地上管線和埋地管線兩種。由于按照原來的止裂預(yù)測(cè)方法己經(jīng)不能保證現(xiàn)代高強(qiáng)度高韌性管線的延性斷裂止裂性能,20世紀(jì)80年代美國(guó)天然氣協(xié)會(huì)AGA委托包括美國(guó)SwRI和意大利CSM在內(nèi)的多家機(jī)構(gòu)進(jìn)行了合作研究,試圖得到一種理論上可靠,實(shí)驗(yàn)證明可行的防止管線延性斷裂長(zhǎng)程擴(kuò)展的方法。
歐洲管線研究組織EPRG也在20世紀(jì)70年代進(jìn)行的實(shí)物實(shí)驗(yàn)的基礎(chǔ)上從1983年開始對(duì)高韌性的管線鋼管進(jìn)行了大量的實(shí)物實(shí)驗(yàn),并于1995年公布了高強(qiáng)度管線鋼止裂韌性推薦值,1996年制定的1502183-3管線鋼管技術(shù)條件采用了EPRG的推薦值。1985年日本幾大鋼鐵公司聯(lián)合進(jìn)行了一次較大規(guī)模的實(shí)物實(shí)驗(yàn),基于Maxey的雙曲線法對(duì)實(shí)驗(yàn)結(jié)果進(jìn)行了分析,得到了有價(jià)值的結(jié)論。
下面結(jié)合兩次大規(guī)模全尺寸實(shí)驗(yàn)寶貴的完整數(shù)據(jù)對(duì)全尺寸實(shí)驗(yàn)測(cè)試情況進(jìn)行說明,其中真實(shí)斷裂速度與CVN韌性止裂預(yù)測(cè)是本文重點(diǎn)關(guān)注的對(duì)象。
3.2.1.1北美聯(lián)盟管道全尺寸爆破實(shí)驗(yàn)
北美聯(lián)盟管道總投資30億美元,由6家公司合資興建,全長(zhǎng)2627km,從加拿大的British Columbia到美國(guó)的Illinois,計(jì)劃2000年投入運(yùn)營(yíng)。該管道設(shè)計(jì)輸送能力為每天375×105m3,主干線設(shè)計(jì)最大輸送壓力為12MPa,管徑9l4mm;支線管徑1067mm,最大設(shè)計(jì)壓力為8.274MPa。
聯(lián)盟管道的設(shè)計(jì)在幾個(gè)方面都創(chuàng)造了新的世界水平:
高韌性管線鋼管——CVN沖擊韌性高于217J;
高的操作壓力——最大操作壓力12MPa;
富氣輸送——含15%乙烷,3%丙烷,天然氣最大熱值為44.2MJ/m3。
為了驗(yàn)證聯(lián)盟管道Φ914和Φ1067鋼管的止裂韌性,進(jìn)行了兩組全尺寸瀑破實(shí)驗(yàn),實(shí)驗(yàn)管段全長(zhǎng)約366m,中間為9根11m長(zhǎng)的實(shí)驗(yàn)樣管,爆破實(shí)驗(yàn)時(shí)裂紋將在其中進(jìn)行擴(kuò)展。實(shí)驗(yàn)樣管沿東西方向分別標(biāo)為1E、2E以及1W、2W等,預(yù)制裂紋穿過1E和1W之間的環(huán)焊縫。第一次實(shí)驗(yàn)的示意圖如圖3-5所示。
表3-l給出了各實(shí)驗(yàn)管段的標(biāo)準(zhǔn)夏比沖擊功以及按照實(shí)驗(yàn)工況用Maxey雙曲線法預(yù)測(cè)的止裂韌性數(shù)值。
表3-l聯(lián)盟管道爆破實(shí)驗(yàn)夏比沖擊能量數(shù)值(單位:J)
鋼管編號(hào) |
第一次實(shí)驗(yàn) |
第二次實(shí)驗(yàn) |
2W |
1W |
1E |
2E |
2W |
1W |
1E |
2E |
鋼管東端沖擊功 |
237 |
178 |
185 |
231 |
217 |
184 |
203 |
247 |
鋼管西端沖擊功 |
253 |
181 |
184 |
223 |
223 |
204 |
185 |
226 |
預(yù)測(cè)止裂沖擊功 |
195 |
223 |
第一次爆破實(shí)驗(yàn)采用Φ914鋼管,壁厚14.2mm,鋼級(jí)X70,操作壓力12MPa,實(shí)驗(yàn)溫度23.8℃,天然氣熱值為44.6MJ/m3。
通過炸藥爆破法,裂紋穿過1E和1W中間環(huán)裂縫,并在鋼管頂端開始擴(kuò)展。第一次爆破實(shí)驗(yàn)中實(shí)驗(yàn)斷口均為韌性斷裂,在樣管1W中,裂紋沿軸向直線擴(kuò)展,在樣管1E中,裂紋沿軸向直線擴(kuò)展將近鋼管末端時(shí),其擴(kuò)展方向稍有傾斜,但在1W和1E中均未發(fā)生止裂。在1W樣管的末端,裂紋穿過環(huán)焊縫直接進(jìn)入2W樣管中繼續(xù)直線擴(kuò)展約2m后轉(zhuǎn)向并繞鋼管環(huán)向擴(kuò)展一圈后止裂,環(huán)向的一圈裂紋將實(shí)驗(yàn)管線分割成東西兩部分。在1E樣管的東端,在距離1E、2E環(huán)焊縫0.5m的地方,裂紋由軸向直線擴(kuò)展轉(zhuǎn)化為撕裂型剪斷擴(kuò)展,隨后擴(kuò)展進(jìn)入2E樣管(螺旋縫焊管)中,呈螺旋線沿2E樣管向前擴(kuò)展,裂紋擴(kuò)展方向垂直于樣管的螺旋焊縫,在裂紋螺旋狀前進(jìn)約4.25圈后止裂。
第二次爆破實(shí)驗(yàn)是為了模擬Φ1067鋼管的止裂過程,由于實(shí)驗(yàn)設(shè)備不到位,最終仍采用功914鋼管,壁厚14.2mm,鋼級(jí)X70,操作壓力12MPa,實(shí)驗(yàn)溫度16.5℃。通過雙曲線法判定止裂韌性與試圖模擬的鋼管相同。
實(shí)驗(yàn)二的斷口均為剪切斷裂,裂紋擴(kuò)展長(zhǎng)度為33.6m。由于1W和1E沖擊功低于預(yù)測(cè)的止裂沖擊韌性,因而裂紋均沿1W和lE軸向直線擴(kuò)展并分別進(jìn)入2W和2E樣管,最后在2W和2E樣管中止裂,如圖3-6所示。
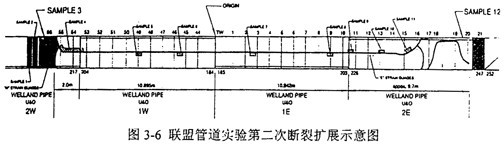
在2E樣管中,裂紋直線擴(kuò)展約4.5m后開始轉(zhuǎn)彎沿螺旋線擴(kuò)展。當(dāng)遇到直焊縫后又產(chǎn)生一個(gè)二次裂紋,二次裂紋沿直焊縫擴(kuò)展約1m后也開始轉(zhuǎn)向沿螺旋線擴(kuò)展。當(dāng)主裂紋第二次遇到直焊縫時(shí),先沿直焊縫擴(kuò)展lm多長(zhǎng)然后轉(zhuǎn)向擴(kuò)展并隨即止裂。
斷裂擴(kuò)展全程將壓力傳感器采集的壓力數(shù)據(jù)與上述斷裂擴(kuò)展速度繪制成壓力一速度曲線,根據(jù)Maxey雙曲線法做出了止裂韌性的預(yù)測(cè)。在考慮Leis修正(3-9式)的基礎(chǔ)上,該預(yù)測(cè)與實(shí)驗(yàn)結(jié)果吻合良好。
3.2.1.2日本HLP組織實(shí)驗(yàn)
1978年,日本鋼鐵學(xué)會(huì)(ISIJ)成立了高強(qiáng)度輸送管HLP(High-strength Line Pipe)專業(yè)研究委員會(huì)。該組織在1978-1983年間進(jìn)行了七次全尺寸爆破實(shí)驗(yàn),其中五次在Kamaishi(釜石,編號(hào)A1、A2、A3、Bl、B2),兩次在BGC(英國(guó)天然氣公司,British Gas CoMPany,編號(hào)Cl、C2)。
實(shí)驗(yàn)材料是經(jīng)控軋(Controlled-Rolled)或調(diào)質(zhì)(Quenched and Tempered)工藝制造的APIX70管,直徑1219mm,壁厚18.3mm。A和B系列實(shí)驗(yàn)采用空氣作為壓縮氣體,實(shí)驗(yàn)溫度在3℃到12℃之間。C系列實(shí)驗(yàn)采用天然氣(富氣),實(shí)驗(yàn)溫度為-5℃。實(shí)驗(yàn)用管道氣壓除C2外均為11.6MPa,C2采用10.4MPa。
每段鋼管長(zhǎng)約10m,每組實(shí)驗(yàn)采用7段管材環(huán)縫焊接,并在每端焊上壁厚為26.67mm的蓄氣管,全長(zhǎng)約150m。實(shí)驗(yàn)管段置于地下l.3m深處,除蓄氣管外的部分回填上砂子。實(shí)驗(yàn)外觀形貌如圖3-7所示。
裂紋的爆破源是一條500mm長(zhǎng)沿軸向切割的穿透裂紋,設(shè)置在裂紋起始管CIP(Crack Initial Pipe)的中心,兩側(cè)管段按南北方向分別標(biāo)號(hào)為S3、S2、S1和Nl、NZ、N3。在裂紋擴(kuò)展期間,測(cè)量了裂紋擴(kuò)展速率、壓力降低和應(yīng)變變化。
實(shí)驗(yàn)采用了大量不同韌性的鋼管,按照一定的順序排列。
A系列實(shí)驗(yàn)中,裂紋沿夏比沖擊能量CKV值約為50J的起裂管CIP,依次穿過韌性值遞增排列的鋼管。各管段的大致韌性值是在每次爆破實(shí)驗(yàn)后經(jīng)過精心研究確定的。A3中Sl到S2是唯一的例外;
B系列實(shí)驗(yàn)中,起裂管兩側(cè)同一方向的管段韌性值大致相同,是為了研究?jī)筛L(zhǎng)范圍內(nèi)具有相同價(jià)F值的管子的裂紋擴(kuò)展行為,兩側(cè)夏比沖擊功預(yù)設(shè)為120J和150J。另外,B系列實(shí)驗(yàn)中起裂管CIP的韌性較高(CKV約90J),長(zhǎng)度較長(zhǎng)(約16m),以減輕起裂過程對(duì)實(shí)驗(yàn)段的影響;
在C系列實(shí)驗(yàn)中,因壓縮氣體為多種成份的天然氣,在開裂減壓時(shí)將引起相變,阻礙了氣體的逸出,使止裂變得困難,因而普遍選用了高韌性鋼管。
管道排列順序和各段對(duì)應(yīng)的夏比沖擊功價(jià);CKV、標(biāo)準(zhǔn)DWTT功DS和預(yù)開裂DWTT功DP如表3-2所示。
表3-2日本HLP管道爆破實(shí)驗(yàn)各段CVN與DWTT吸收功(單位:J)
實(shí)驗(yàn)號(hào) |
實(shí)驗(yàn)溫度 |
類目 |
S3 |
S2 |
S1 |
CIP |
N1 |
N2 |
N3 |
S |
N |
A1 |
+12 |
材質(zhì) |
控軋 |
控軋 |
控軋 |
控軋 |
調(diào)質(zhì) |
調(diào)質(zhì) |
— |
CKV |
202 |
140 |
83 |
51 |
92 |
188 |
— |
DS |
47050 |
7920 |
5230 |
2650 |
4510 |
8820 |
— |
DP |
4210 |
5120 |
3590 |
2070 |
3160 |
4610 |
— |
A2 |
+3 |
材質(zhì) |
控軋 |
控軋 |
控軋 |
控軋 |
控軋 |
控軋 |
控軋 |
CKV |
196 |
139 |
119 |
45 |
108 |
169 |
275 |
DS |
6760 |
6170 |
5980 |
2760 |
6250 |
9090 |
1077 |
DP |
4210 |
3850 |
3790 |
2270 |
4200 |
4580 |
582 |
A3 |
+8 |
材質(zhì) |
控軋 |
控軋 |
控軋 |
控軋 |
調(diào)質(zhì) |
調(diào)質(zhì) |
控軋 |
CKV |
209 |
103 |
127 |
51 |
122 |
153 |
202 |
DS |
5120 |
4430 |
6270 |
2530 |
424 |
758 |
8820 |
DP |
3650 |
3110 |
4150 |
1940 |
3310 |
4490 |
4660 |
B1 |
+6 |
材質(zhì) |
— |
控軋 |
控軋 |
控軋 |
控軋 |
控軋 |
控軋 |
— |
CKV |
— |
126 |
124 |
76 |
79 |
155 |
156 |
— |
DS |
— |
5170 |
6040 |
4080 |
4200 |
7350 |
7460 |
— |
DP |
— |
4250 |
4230 |
3030 |
3180 |
4430 |
4470 |
— |
B2 |
+12 |
材質(zhì) |
— |
控軋 |
控軋 |
控軋 |
控軋 |
調(diào)質(zhì) |
調(diào)質(zhì) |
— |
CKV |
— |
145 |
118 |
93 |
99 |
125 |
129 |
— |
DS |
— |
7350 |
4840 |
5340 |
4800 |
5560 |
5660 |
— |
DP |
— |
4270 |
3390 |
3430 |
3320 |
4200 |
4020 |
— |
C1 |
-5 |
CKV |
341 |
260 |
244 |
203 |
208 |
206 |
324 |
DP |
— |
— |
— |
3990 |
— |
— |
— |
C2 |
-5 |
CKV |
— |
— |
338 |
186 |
232 |
237 |
— |
DP |
— |
— |
— |
5180 |
— |
— |
— |
在全部七次HLP實(shí)驗(yàn)中,裂紋擴(kuò)展與止裂的情況如圖3-8所示。
在圖3-8的所有實(shí)驗(yàn)中,裂紋以全延性方式向?qū)嶒?yàn)管兩端呈軸向擴(kuò)展,并突然轉(zhuǎn)向周向,隨即止裂。這表明管道本身的韌性導(dǎo)致止裂。
3.2.3速度觀測(cè)結(jié)果
在全尺寸爆破實(shí)驗(yàn)中,可以根據(jù)時(shí)線記錄的數(shù)據(jù)計(jì)算裂紋沿鋼管軸向的擴(kuò)展速度。圖3-9和3-10分別在聯(lián)盟管道第一次和第二次實(shí)驗(yàn)的斷裂速度曲線。
從圖中可以看到,在裂紋長(zhǎng)度不超過三倍管道直徑的超始擴(kuò)展階段,因鋼管內(nèi)的氣壓來不及釋放而裂紋加速較快;
在裂紋擴(kuò)展長(zhǎng)度相當(dāng)于第四個(gè)管道直徑長(zhǎng)度的范圍內(nèi),鋼管裂口張開,氣體壓力迅速衰減,直至與裂紋擴(kuò)展速度達(dá)到平衡,此階段斷裂速度先升后降;
隨著裂紋的進(jìn)一步擴(kuò)展,擴(kuò)展過程的參數(shù)包括裂紋擴(kuò)展速度以及裂紋尖端的應(yīng)力取決于鋼管的斷裂韌性。
圖3-11、圖3-12表示日本HLP實(shí)驗(yàn)中裂紋擴(kuò)展速率隨擴(kuò)展距離的變化,空心點(diǎn)為實(shí)測(cè)值。通過對(duì)易發(fā)生斷口分離(斷口分離現(xiàn)象將在下一章中介紹)的控軋(CR)鋼和調(diào)質(zhì)(QT)鋼兩種材料的臨界止裂韌性的測(cè)試,沒有發(fā)現(xiàn)大的差異,說明斷口分離現(xiàn)象對(duì)動(dòng)態(tài)延性斷裂的止裂能力影響不大。
速度曲線表明,在A類實(shí)驗(yàn)中,裂紋起裂后,在韌性較低的CIP擴(kuò)展速度達(dá)以300m/s以上。裂紋進(jìn)入實(shí)驗(yàn)管后,裂紋擴(kuò)展速度隨著裂紋的擴(kuò)展而下降,實(shí)驗(yàn)A3的南側(cè)有例外,裂紋從S1到S2管裂紋擴(kuò)展速度增大,這是由于韌性排列時(shí)S2管的韌性例外地比S1低。在B類實(shí)驗(yàn)中,CIP管的最大裂紋擴(kuò)展速度率為300m/s(B1)和270m/s(B2),這與其韌性較高有關(guān)。
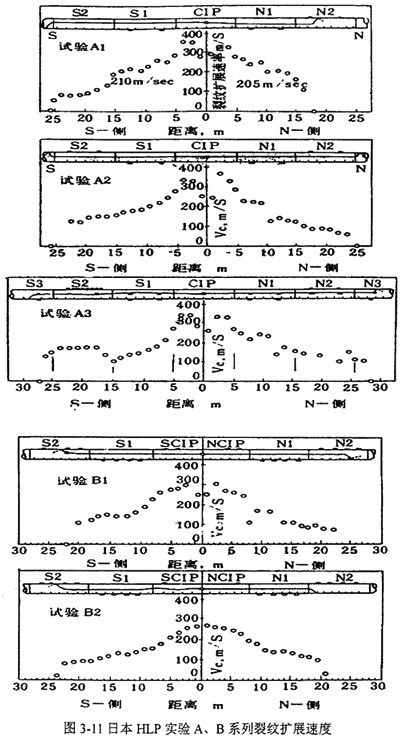
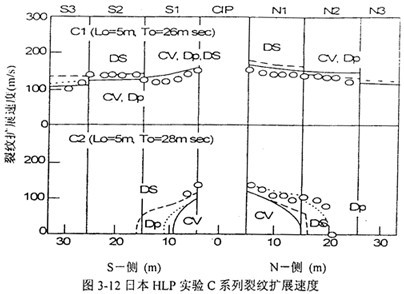
3.2.4從全尺寸實(shí)驗(yàn)中得到的結(jié)論
本節(jié)介紹了現(xiàn)有的基于全尺寸實(shí)驗(yàn)的止裂韌性判定方法,搜集整理了國(guó)際上兩次著名的大規(guī)模鋼制輸氣管道全尺寸實(shí)驗(yàn)的進(jìn)行情況和各管段材料性能以及實(shí)測(cè)裂紋擴(kuò)展速度數(shù)據(jù)。以下幾點(diǎn)與論文密切相關(guān):
首先,管道斷裂動(dòng)力學(xué)上的有限元法是近十幾年隨計(jì)算機(jī)的發(fā)展而蓬勃興起的技術(shù),其精確程度與具體設(shè)計(jì)參數(shù)下的可靠性還有待在進(jìn)一步的實(shí)踐中證實(shí)。在此背景下,國(guó)際上已經(jīng)沿用了近三十年的全尺寸實(shí)驗(yàn)確定管道止裂韌性的方法無疑為計(jì)算提供了很好的原始數(shù)據(jù)與結(jié)果比較;
其次,我國(guó)目前尚沒有進(jìn)行高壓輸氣管道的全尺寸爆破實(shí)驗(yàn),國(guó)外的實(shí)驗(yàn)我們可以得到的數(shù)據(jù)十分有限,因而顯得彌足珍貴。具體的實(shí)測(cè)數(shù)據(jù),只有和實(shí)驗(yàn)條件,設(shè)計(jì)參數(shù),各段鋼材性能等參數(shù)結(jié)合起來才有參考價(jià)值;最后,也是最重要的一點(diǎn),雙曲線法在結(jié)合全尺寸實(shí)驗(yàn)在預(yù)測(cè)高韌性管道止裂韌性時(shí)已發(fā)生巨大的偏差,如圖3-4所述。究其原因,本文認(rèn)為很大程度上是由于高韌性鋼材的明顯的塑性功耗散現(xiàn)象己經(jīng)使全尺寸實(shí)驗(yàn)的結(jié)果背離了雙曲線法止裂分析的初衷。這正是本章計(jì)算試圖解決的問題。
對(duì)于最后一點(diǎn),具體解釋如下:
傳統(tǒng)分析氣體爆破實(shí)驗(yàn)的方法是將實(shí)驗(yàn)管分成兩組,即“擴(kuò)展組”和“止裂組”,它們?nèi)Q于裂紋順利通過管道還是在管道內(nèi)止裂,然后在兩者之間求出沖擊韌性臨界值。這種做法的正確性是建立在動(dòng)態(tài)裂紋擴(kuò)展速率在同一韌性的鋼管中基本不變,且不會(huì)明顯受到管道接頭部位的影響的前提下的。但現(xiàn)有的高韌性管道實(shí)驗(yàn)數(shù)據(jù)表明,在韌性一致的管段中,也會(huì)發(fā)生斷裂擴(kuò)展速度逐漸減慢直至止裂的現(xiàn)象。對(duì)于高韌性鋼管,這種效應(yīng)尤其明顯。這一結(jié)論可以從上兩節(jié)的實(shí)驗(yàn)數(shù)據(jù)中得到證實(shí),例如:
所有實(shí)驗(yàn)的止裂都不是在同一管段內(nèi)部發(fā)生的,任意管段內(nèi)均發(fā)生了減速。尤其是HLP組織的B類實(shí)驗(yàn):在Bl的兩側(cè),B2的北側(cè),裂紋從CIP起裂后經(jīng)過的兩段管子韌性相差無幾,卻均在第一段中持續(xù)擴(kuò)展而在第二段中止裂。
這說明止裂與否不僅取決于管段的韌性,還取決于裂紋進(jìn)入管段的速度,以及裂紋在管段內(nèi)擴(kuò)展的距離。也就是說,對(duì)于斷裂韌性高于一定數(shù)值的管道,只要長(zhǎng)度足夠,就必然會(huì)發(fā)生止裂。因而,對(duì)應(yīng)于某種韌性,僅有是否止裂的結(jié)論是不夠的,止裂長(zhǎng)度概念的引入十分必要。
從本節(jié)的討論看出,高韌性管線中裂紋止裂韌性的臨界值取決于要求的止裂長(zhǎng)度。這需要建立新的能夠考慮到止裂長(zhǎng)度影響的模型。對(duì)于動(dòng)態(tài)裂紋擴(kuò)展的有限元算法,要考慮韌性導(dǎo)致的減速行為,應(yīng)將實(shí)驗(yàn)可測(cè)的韌性作為參數(shù)代入,在數(shù)值模擬中起到減速的作用。
3.3實(shí)測(cè)減速模型
通過上一節(jié)對(duì)全尺寸實(shí)驗(yàn)中減速現(xiàn)象的描述,很容易想到的解決方法是直接利用實(shí)測(cè)速度曲線,對(duì)具體應(yīng)用的管道裂紋擴(kuò)展速度規(guī)律做參數(shù)擬合,進(jìn)而進(jìn)行有限元計(jì)算。實(shí)測(cè)減速模式正是基于這種思路。
3.3.1實(shí)測(cè)減速模型的描述
一般地,對(duì)管線裂紋擴(kuò)展速度變化,采用(3-10)式進(jìn)行擬合:
式中助是擬合段曲線的初速度,Lr表示該初速度下的止裂長(zhǎng)度,z表示裂尖位置。對(duì)于圖3-9中的lW段,取v0=200m/s,Lr=35m,擬合結(jié)果如圖3-13所示:
考慮到影響管道裂紋擴(kuò)展速度變化的參數(shù)主要有管道內(nèi)部氣體壓力p0,管道的直徑D和管道的壁厚h,和管道動(dòng)態(tài)斷裂強(qiáng)度和韌性參數(shù)等,可分別定義v0和Lr為:
其中pa為大氣壓力,σf為流動(dòng)應(yīng)力,等于屈服應(yīng)力和拉伸強(qiáng)度的平均值;CV為CVN實(shí)驗(yàn)測(cè)得的夏比沖擊功,k1和k2分別是具有長(zhǎng)度量綱的常數(shù),由實(shí)驗(yàn)歸納得到。
3.3.2實(shí)測(cè)減速模型的不足
作者曾在(3-10)至(3-12)的基礎(chǔ)上,與唐甜合作,對(duì)西氣東輸管線進(jìn)行了評(píng)估。本文的重點(diǎn)不在于此,因而不再重復(fù)。
實(shí)測(cè)減速模型畢竟僅僅基于經(jīng)驗(yàn)公式,缺乏足夠的理論基礎(chǔ)。其主要的表達(dá)式(3-10)至(3-12)成立的依據(jù)還存在一些不確定的因素,k1和k2的數(shù)值通過現(xiàn)有的全尺寸實(shí)驗(yàn)數(shù)據(jù)也難以定為常數(shù),只給出大致的量級(jí)范圍。另外,指定裂紋速度變化的規(guī)律之后再判斷裂紋是否止裂,不足以單獨(dú)用作工程上判斷管道止裂性能的憑據(jù)。
3.4韌性減速機(jī)理
本節(jié)以裂紋擴(kuò)展過程中整體及裂紋尖端區(qū)域的能量平衡方程為出發(fā)點(diǎn),應(yīng)用流變斷裂學(xué)中的基本原理,得到宏觀唯象形式的表達(dá),并應(yīng)用于有限元模型。其中表示材料韌性的關(guān)鍵參數(shù)通過改進(jìn)后的小試件實(shí)驗(yàn)得到,個(gè)別關(guān)鍵系數(shù)通過全尺寸實(shí)驗(yàn)的檢驗(yàn)確定。
3.4.1含裂紋的鋼制管道能量平衡方程
按照流變斷裂學(xué)的觀點(diǎn),不可逆的裂紋擴(kuò)展區(qū)別于受絕熱或等溫變形約束的理想彈性體的重要特征是開裂物體的墑增現(xiàn)象,因而采用包括描述熵增、熱膨脹、熱傳導(dǎo)等過程所需的七個(gè)參數(shù)來描述裂紋擴(kuò)展過程。
裂紋體的整體能量平衡意味著動(dòng)能時(shí)間變化率與內(nèi)能時(shí)間變化率的總和等于全部力與力偶的功率及單位時(shí)間內(nèi)流進(jìn)或流出物體全部其余能量(對(duì)于本文問題僅考慮熱能)的總和。也就是說,作用于物體上的功增量δW與物體吸收或散逸的熱能增量δ 的總和等于物體的內(nèi)能增量△U與動(dòng)能增量△K的總和,即:
△K+△U=δW+δ

(3-13)
式中動(dòng)能和內(nèi)能均是可加和的狀態(tài)函數(shù),僅與初始態(tài)和終結(jié)態(tài)有關(guān)。但功和熱還與過程有關(guān),為此采用了△和δ兩種增量記號(hào)。
若增量無窮小,且方程中的物理量對(duì)于時(shí)間是可微函數(shù),則式(3-13)可以寫成對(duì)時(shí)間t的微分形式:

(3-14)
由于動(dòng)能和內(nèi)能是可加和函數(shù),故有:
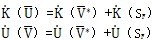
(3-15a)
(3-15b)
式中

和S
F分別為管道所占空間域和裂紋擴(kuò)展引起的新表面, 是二者之差。若令新裂紋面的能量變化率為:

(3-16)
則可得到:

(3-17)
將上式寫成微分形式:

(3-18)
式(3-18)中,W表示外力功,U表示應(yīng)變能,K表示動(dòng)能,Γ表示表面能,

表示熱量引起的能量損失。(

)表示除去裂紋擴(kuò)展形成的新表面以外的部分的值。
下面考慮單側(cè)裂紋擴(kuò)展的全管道模型,即圖2-6中1/4管道模型的兩倍。
令Λ=-

,表示由于塑性功卸載引起的熱耗散量,并將Λ和Γ分別寫成塑性功率λ與表面能密度y與裂紋擴(kuò)展導(dǎo)致新生成表面面積的乘積:
Λ=2ahλ,Γ=2ahy (3-19)
式中a表示裂紋單向擴(kuò)展長(zhǎng)度,h表示厚度。
定義裂紋單側(cè)擴(kuò)展的驅(qū)動(dòng)力G:
一般可設(shè)鋼材的表面密度y為材料常數(shù),同時(shí)注意這里λ與Gd均是與裂紋擴(kuò)展速率v相關(guān)的量。對(duì)于瞬態(tài)擴(kuò)展,某時(shí)刻的斷裂韌性Gd可以表示為:
對(duì)于金屬材料,λ通常比y大三個(gè)數(shù)量級(jí),故y可忽略不計(jì)。
在裂紋擴(kuò)展的過程中,局部能量不守恒。此時(shí)的管道裂紋尖端可視作為一個(gè)熱源匯,為裂紋的擴(kuò)展積累和提供能量,并遵循G=Gd的關(guān)系。
由(3-14)和(3-21)式,最終得到裂紋單側(cè)擴(kuò)展的能量平衡方程:
式(3-22)中da/dt=vt表示t時(shí)刻管道裂紋的瞬時(shí)擴(kuò)展速度。
從以上推導(dǎo)可以看出,輸入功率dW/dt一定的情況下,熱耗散率λ起到了制約動(dòng)能K的作用。裂紋擴(kuò)展過程必然伴隨有熱傳導(dǎo)和墑產(chǎn)生,對(duì)于耗散型材料(如高韌性鋼),熱耗散效應(yīng)不容忽視。
3.4.2有限元中的速度反饋機(jī)制
首先給出第二章的有限元漠型中時(shí)間步長(zhǎng)為n時(shí)的各能量求解表達(dá)式。
外力功表達(dá)式為:
W
0=0,W
n=W
n-1+

(d
n-d
n-1) (3-23)
式中d為節(jié)點(diǎn)上的位移分量,

為作用在節(jié)點(diǎn)上的外力。
在時(shí)間步為n時(shí)的動(dòng)能表達(dá)式為:
式中i為節(jié)點(diǎn)號(hào),M是集中于節(jié)點(diǎn)處的質(zhì)量,I是集中于節(jié)點(diǎn)處的轉(zhuǎn)動(dòng)慣量,vn是節(jié)點(diǎn)的線速度分量,ωn是節(jié)點(diǎn)的角速度分量。
在時(shí)間步為n時(shí)的應(yīng)變能表達(dá)式為:
式中h是單元厚度,

是單元面積,σ和ε是單元的應(yīng)力和應(yīng)變。
設(shè)時(shí)間步為n,迭代步為k,對(duì)于任意的變量E ,以△

表示

。
根據(jù)上一節(jié)所得到的式(3-22),在有限元計(jì)算中引入速度反饋機(jī)制。注意到(3-23)到3-25)式均為圖2-6中1/4管道模型下的值,相當(dāng)于上一小節(jié)中相應(yīng)物理量的一半,驗(yàn)算下式:

(3-26)
式中η表示能量平衡迭代要求的精度,0<η<l,越接近于零表示精度越高。若(3-26)式成立,則進(jìn)入n+1時(shí)間步計(jì)算;若不成立,則進(jìn)入k+1迭代步:
以得到的

為新的試算速度進(jìn)行迭代,直至(3-26)式滿足。
(3-27)式具有其確切的物理意義,即:
若(l-η)△

>△

+△

+0.5hG
dn△

,表示外力功過剩。過剩的部分將通過(3-27)式轉(zhuǎn)化為動(dòng)能;
若(l+η)△

>△

+△

+0.5hG
dn△

,則表示外力不足以抵消斷裂韌性及應(yīng)變能變化,這時(shí)需要犧牲動(dòng)能來保證裂紋擴(kuò)展。
在式(3-27)中,以裂尖速率替代了管道整體平均速率反映動(dòng)能帶來的影響?紤]到二者趨勢(shì)上的一致性,并因等式左端的

是試算值,僅影響到計(jì)算速度與收斂性,而不影響計(jì)算精度,故可暫作此假定。
速度反饋機(jī)制的收斂性同網(wǎng)格疏密程度,時(shí)間步長(zhǎng),試算初速度等相關(guān)。它在程序中實(shí)現(xiàn)的流程如圖3-14所示。
裂紋體的殘余動(dòng)能并不能全部用于驅(qū)動(dòng)裂紋擴(kuò)展,因?yàn)橄喈?dāng)一部分動(dòng)能包含在裂紡頂端后面較遠(yuǎn)的區(qū)域內(nèi)。Hahn(1973)對(duì)雙懸臂梁試樣的測(cè)試表明,約有85%的動(dòng)能消耗于裂紋驅(qū)動(dòng)能。修正后的(3-27)可以表示為:
至此,韌性減速機(jī)理已經(jīng)基本建立。但(3-26)式中表示動(dòng)態(tài)斷裂韌性的關(guān)鍵量Gd的確定方法尚未解決。下面-小節(jié)我們將就此展開討論。
3.4.3小試樣沖擊實(shí)驗(yàn)與Gd的關(guān)系
工程上廣泛使用小試件沖擊實(shí)驗(yàn)的辦法測(cè)定管道材料的動(dòng)態(tài)斷裂韌性,具體測(cè)試手段與結(jié)果在第四章另有詳述。
本小節(jié)的目的是通過小試樣沖擊實(shí)驗(yàn)的設(shè)計(jì)參數(shù)和測(cè)得的吸收功,給出韌性減速機(jī)理中代表動(dòng)態(tài)斷裂韌性的關(guān)鍵量Gd的基本表達(dá)。
2.1.4節(jié)已經(jīng)提到,動(dòng)態(tài)斷裂韌性Gd除與材料的性質(zhì)密切相關(guān)外,還與環(huán)境溫度,應(yīng)力狀態(tài),試件厚度,特別是斷裂速度關(guān)系密切。
因小試件沖擊實(shí)驗(yàn)與管道全尺寸裂紋擴(kuò)展的相似性,忽略應(yīng)力狀態(tài)對(duì)斷裂韌性的影響。設(shè)小試件沖擊實(shí)驗(yàn)中的特定參數(shù)為試件厚度h0,沖擊速度v0,實(shí)驗(yàn)環(huán)境溫度T0,韌帶寬度即裂紋擴(kuò)展長(zhǎng)度a0,測(cè)到的外力吸收功為W0。
由忽略表面能的(3-21)式,小試件裂紋擴(kuò)展中的動(dòng)態(tài)斷裂韌性Gd0?杀硎緸椋
式中λ為材料的塑性功率,v為瞬時(shí)擴(kuò)展速率,a為瞬時(shí)裂紋長(zhǎng)度,O<a<a0。注意這里裂紋每擴(kuò)展da,新增裂紋面面積為2hda。
考慮裂紋擴(kuò)展過程中的某微小時(shí)間增量dt,對(duì)小試樣沖擊的實(shí)驗(yàn)過程應(yīng)用能量平衡方程(3-22)式并對(duì)裂紋擴(kuò)展全過程在時(shí)間上進(jìn)行積分:
式中△W、△U、△K分別為裂紋擴(kuò)展過程中試件消耗的外力功、應(yīng)變能增量和動(dòng)能增量,WC為裂紋開裂過程消耗的起裂功。對(duì)于高韌性鋼,△U、△K可忽略。
因小試件試樣斷裂時(shí)間很短,可假定起裂后的斷裂速度始終等同于擺錘的沖擊速度v0。另外考慮在試樣尾部因裂紋前端發(fā)生塑性形變的范圍變短,Gd會(huì)相應(yīng)有所損失,令這-部分損失的能量為P(h0,T0,v0),則:
式(3-31)可以作為確定式(3-26)至式(3-28)中Gd(h,T,v)的依據(jù)。
3.4.4待定參數(shù)的確定
式(3-31 )留下了W
e和P兩個(gè)參數(shù)有待確定。根據(jù)其物理意義,可以通過預(yù)制裂紋、脆化缺口等方法消除W
e的影響。雙試件實(shí)驗(yàn)更可以達(dá)到雙重目的,通過兩次不同韌帶寬度a
1和a
2的試件(其余條件完全相同)的實(shí)測(cè)吸收功W
1,W
2之差,可以直接得到G
d0:
因?yàn)橛绊戫g性的參數(shù)比較復(fù)雜,最可靠的做法是采用和真實(shí)管道同樣的壁厚,在一系列溫度和沖擊速度下用雙試件法測(cè)定斷裂韌性,以備計(jì)算采用。
3.5基于韌性減速機(jī)理的算例分析
韌性減速機(jī)理應(yīng)用于有限元計(jì)算后,可以方便地隨意指定計(jì)算區(qū)域內(nèi)的管道裂紋的初速度v0,通過第四章的小試件方法測(cè)到的動(dòng)態(tài)斷裂韌性Gd,模擬整個(gè)管道包括速度變化的曲線在內(nèi)的真實(shí)開裂情況。
本文通過上述方法,對(duì)圖3-9至圖3-12中的全尺寸實(shí)測(cè)斷裂速度曲線結(jié)果進(jìn)行了校核,得到了比較吻合的結(jié)果,F(xiàn)以聯(lián)盟管道第一次實(shí)驗(yàn)IE段為例,設(shè)定擴(kuò)展的初速度為330m/s,速度變化的計(jì)算值同實(shí)驗(yàn)對(duì)比如圖3-15所示:
通過大量的測(cè)算與歸納,得到吻合較好時(shí)的Gd與CVN能量的關(guān)系:
Gd=1.3CKV=0.016CKV (3-33)
式中cKV和CKV分別是單位面積標(biāo)準(zhǔn)夏比沖擊韌性值和標(biāo)準(zhǔn)夏比沖擊功,cKV=CKV/(hoao),對(duì)于標(biāo)準(zhǔn)CVN試件,h0=10mm,a0=8mm。
另外,當(dāng)斷裂速度降至低于100m/s時(shí),要考慮偏隨速度的降低:
當(dāng)v<100m/s,Gd=o.8cKV+0.5cKV·v/100 (3-34)
直至止裂時(shí)Gd降為止裂韌性0.8cKV。
(3-33)和(3-34)式中的系數(shù)1.3和O.8的獲得方法為大量試算后取與全尺寸速度實(shí)測(cè)結(jié)果普遍吻合較好的值。
根據(jù)圖3-16中的MISES應(yīng)力分布可以判斷裂尖處的塑性區(qū)范圍。隨著裂紋擴(kuò)展過程中韌性導(dǎo)致的速度降低,塑性區(qū)的范圍逐漸縮小。
圖3-17和圖3-18是針對(duì)西氣東輸某特定設(shè)計(jì)參數(shù)的管線,應(yīng)用韌性減速機(jī)理計(jì)算時(shí)能量釋放率G和裂紋尖端張開角CTOA的變化。
隨著計(jì)算輸入韌性Gd導(dǎo)致的裂紋不斷減速,G和CTOA衰減幅度明顯,直至止裂。
3.6本章小結(jié)
全尺寸爆破實(shí)驗(yàn)中觀測(cè)到的速度變化表明,對(duì)于高韌性管線,由塑性功耗散引起的動(dòng)能衰減不可忽略。裂紋在低于預(yù)測(cè)斷裂韌性的均質(zhì)管道中也會(huì)發(fā)生明顯的減速現(xiàn)象,直至止裂。Maxey雙曲線法在預(yù)測(cè)高韌性鋼止裂韌性時(shí)發(fā)生的偏差是上述論述的有力旁證。
為此我們引入了依靠全尺寸實(shí)驗(yàn)指定裂紋擴(kuò)展速度變化的實(shí)測(cè)減速模型,將全尺寸實(shí)驗(yàn)的速度歷史通過參數(shù)分析應(yīng)用到待測(cè)管線。因影響裂紋擴(kuò)展速度的原因過于復(fù)雜,這種做法的可靠性不能保證。
本章的主要工作是通過流變斷裂學(xué)的基本理論,推導(dǎo)了對(duì)于瞬態(tài)裂紋擴(kuò)展,動(dòng)態(tài)斷裂韌性在整體能量平衡方程中所起的作用,并在有限元中構(gòu)造了迭代算法。表征材料韌性的參數(shù)GJ(v)通過小試樣實(shí)驗(yàn)確定,在計(jì)算中作為已知函數(shù)代入。
通過和真實(shí)裂紋擴(kuò)展曲線的對(duì)照,建立了通過夏比沖擊功估算GJ的經(jīng)驗(yàn)?zāi)P停?-33)和(3-34),并據(jù)此對(duì)特定參數(shù)的管道進(jìn)行了分析。
夏比沖擊和DWTT實(shí)驗(yàn)測(cè)試的是試樣斷裂的總能量?偰芰堪ㄆ鹆涯、裂紋擴(kuò)展能、塑性變形能和拋擲試樣的動(dòng)能。已有對(duì)DWTT試樣的研究認(rèn)為前兩部分能量占總能量的絕大部分。因而,本文認(rèn)為雙試件DWTT實(shí)驗(yàn)是最合適的小試件測(cè)定Gd(v)的手段。
但對(duì)于大多數(shù)工程情況,該實(shí)驗(yàn)條件難以被滿足。這就需要采用判定動(dòng)態(tài)斷裂韌性的一般方法,如CVN和DWTT,尤其是CVN。這是因?yàn)楣こ躺贤鶄溆懈鞣N溫度下的一系列夏比沖擊能量的數(shù)據(jù)。
在用全尺寸管道實(shí)驗(yàn)的數(shù)據(jù)作校對(duì)的時(shí)候,同樣會(huì)遇到類似的問題。一般情況下關(guān)于管道韌性的數(shù)據(jù)僅有CVN沖擊能量和DWTT吸收功,所以有必要對(duì)這兩種實(shí)驗(yàn)進(jìn)行進(jìn)一步的分析。有關(guān)CVN和DWTT實(shí)驗(yàn)方面的內(nèi)容,尤其是高韌性鋼材的特性和測(cè)試結(jié)果,將在下一章中詳細(xì)討論。