摘要:通過(guò)對(duì)正常齒輪和裂紋齒輪進(jìn)行動(dòng)力學(xué)仿真研究,發(fā)現(xiàn)裂紋齒輪的固有頻率要比正常齒輪有明顯的降低;進(jìn)一步研究裂紋深度對(duì)齒輪動(dòng)力學(xué)特性的影響,提出了一種診斷齒輪裂紋故障的新方法,并用試驗(yàn)驗(yàn)證了該方法的有效性。
關(guān)鍵詞:漸開(kāi)線齒輪;故障建模;裂紋;固有頻率;模態(tài)分析
齒輪傳動(dòng)是機(jī)械傳動(dòng)的主要形式之一,被廣泛地應(yīng)用于冶金、石化、礦山、交通運(yùn)輸?shù)裙I(yè)部門中。但由于齒輪所處的工作環(huán)境惡劣等原因,很容易受到損害和出現(xiàn)故障。據(jù)統(tǒng)計(jì),傳動(dòng)機(jī)械中80%的故障是由齒輪引起的。齒輪的故障將直接影響設(shè)備的安全可靠運(yùn)行,甚至導(dǎo)致整個(gè)系統(tǒng)的癱瘓。因此,對(duì)齒輪的工作狀態(tài)的監(jiān)測(cè)及故障診斷技術(shù)的研究越來(lái)越受到人們的重視。
齒輪的失效形式多種多樣,其中較常見(jiàn)的裂紋失效是比較嚴(yán)重的一種失效形式,裂紋進(jìn)一步擴(kuò)展,就可能導(dǎo)致輪齒疲勞折斷,甚至引起整個(gè)齒輪的完全失效。因此,對(duì)裂紋進(jìn)行故障機(jī)理分析,尋找一種有效的診斷裂紋故障的方法,對(duì)齒輪的故障診斷是相當(dāng)重要的。
長(zhǎng)期以來(lái),人們?cè)邶X根裂紋的診斷方法方面已進(jìn)行了大量的研究,并取得了很多的成果。常規(guī)的診斷方法是振動(dòng)頻譜分析,它以傳統(tǒng)的振動(dòng)理論為依據(jù),利用診斷儀器對(duì)其振動(dòng)的數(shù)據(jù)和波形進(jìn)行采集,然后進(jìn)行分析診斷,找出故障的原因和所在部位。但這樣做的前提條件是故障模型的建立要足夠準(zhǔn)確,才能對(duì)故障狀態(tài)下的振動(dòng)信號(hào)進(jìn)行正確的識(shí)別,這種方式則需要求診斷人員具有較豐富的故障診斷經(jīng)驗(yàn)。
本文從齒輪動(dòng)力學(xué)角度出發(fā),研究了裂紋深度對(duì)齒輪固有頻率的影響,結(jié)果表明,可以將固有頻率作為齒輪裂紋故障的一個(gè)診斷指標(biāo)。同時(shí),通過(guò)文獻(xiàn)可以知道,齒輪的異常振動(dòng)會(huì)激起齒輪本身的固有頻率。因此,如果能夠精確計(jì)算出正常和裂紋齒輪的固有頻率值,并且能夠在齒輪工作的條件下將其提取出來(lái),對(duì)于齒輪的故障診斷工作將有重要的實(shí)際意義。
1齒輪有限元模態(tài)分析
模態(tài)分析主要用來(lái)確定構(gòu)件或系統(tǒng)的振動(dòng)特性即固有頻率和振型。
1.實(shí)體模型的建立
漸開(kāi)線齒輪建模的難點(diǎn)是如何比較精確地反映出漸開(kāi)線廓形和齒根過(guò)渡圓角,為了力求較高的計(jì)算精度,本文采用在ANSYS中直接建模的方式,其操作流程為。
1)編程生成若干齒廓關(guān)鍵點(diǎn);
2)形成一些過(guò)渡曲線關(guān)鍵點(diǎn);
3)連點(diǎn)成線,生成較精確的漸開(kāi)線廓形;
4)鏡像,生成二維完整齒輪模型;
5)拉伸成體;
6)對(duì)模型進(jìn)行網(wǎng)格劃分。
所建立的齒輪模型的幾何參數(shù)為:齒數(shù)Z=20,模數(shù)m=4,齒寬b=10mm。材料屬性為:楊氏彈性模量E=2.09E11N/m2,泊松比μ= 0.259,材料密度ρ=7.85E3kg/m2。在劃分網(wǎng)格時(shí),采用Solid73單元類型和自由網(wǎng)格劃分方法,得到如圖1所示的有限元模型。
文獻(xiàn)在ANSYS環(huán)境下對(duì)齒輪齒根裂紋進(jìn)行了擴(kuò)展模擬,模擬結(jié)果與實(shí)際很吻合。本文在建立裂紋齒輪的模型時(shí),裂紋開(kāi)口方向和裂紋長(zhǎng)度的選取均參照了上述文獻(xiàn)所提出的方法,只不過(guò)考慮到裂紋加工的方便性,用矩形裂紋代替了圓弧裂紋,裂紋的局部放大圖如圖2所示。裂紋齒輪單元類型和網(wǎng)格劃分方式的選取,均同正常齒輪相同。圖中裂紋的深度為5mm,寬度為 0.3mm。
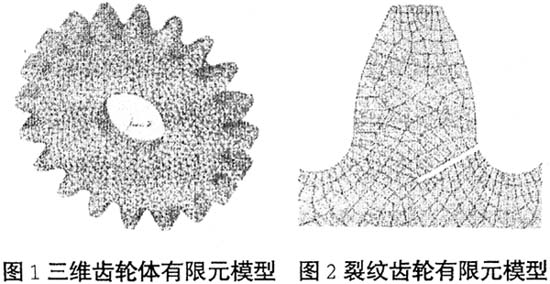
1.2約速及加載
工作條件下,齒輪和傳動(dòng)軸之間為過(guò)盈配合,因此本文的邊界條件約束了齒輪內(nèi)表面各節(jié)點(diǎn)X,Y,Z方向的平動(dòng)自由度和繞X,Y軸的轉(zhuǎn)動(dòng)自由度。模態(tài)是由系統(tǒng)固有特性決定的,與外載荷無(wú)關(guān),因此不需要設(shè)置載荷邊界條件。
1.3結(jié)果分析
本文采用子Block Lanczos法提取了正常齒輪和裂紋齒輪的前10階自由振動(dòng)的模態(tài),由于篇幅限制,表1只列出了前6階固有頻率值。
表1 齒輪的固有頻率值 Hz
模態(tài) |
1 |
2 |
3 |
4 |
5 |
6 |
正常
裂紋 |
293.6
250.1 |
294.8
250.5 |
305.0
262.7 |
337.5
287.5 |
337.7
288.8 |
409.3
400.3 |
從表1可以看出,裂紋齒輪比正常齒輪的固有頻率值明顯降低。
考慮公式

,其中 為固有頻率,K為剛度,M為質(zhì)量。當(dāng)裂紋出現(xiàn)時(shí),齒輪的質(zhì)量并沒(méi)有明顯的改變,所以由公式可以推出, 的降低是由于齒輪剛度的下降引起的,這就是為故障齒輪系統(tǒng)的建模提供了一個(gè)依據(jù)。
2裂紋深度變化對(duì)固有頻率的影響
為進(jìn)一步研究裂紋對(duì)構(gòu)件動(dòng)力學(xué)特性的影響,本文對(duì)齒輪齒根裂紋作了更深入的仿真,仿真過(guò)程主要針對(duì)不同裂紋深度的齒輪展開(kāi)(深度從小到大,共仿真了14組數(shù)據(jù)),對(duì)各齒輪均提取了其前10階固有頻率值。各階固有頻率隨裂紋深度變化的趨勢(shì)圖如圖3所示,其中橫坐標(biāo)代表裂紋深度比(裂紋深度和齒根處齒厚之比);縱坐標(biāo)為裂紋齒輪和正常齒輪的固有頻率比。為便于觀察,本文僅畫出了前7階固有頻率隨裂紋深度變化的趨勢(shì)圖,如圖3所示。
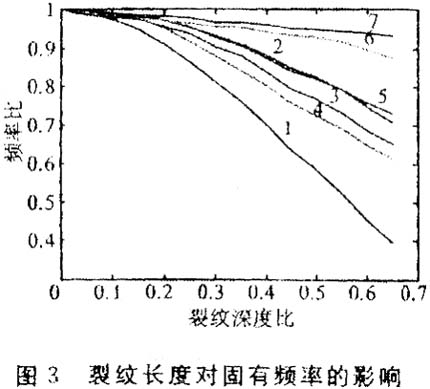
從圖3可以看出,隨著裂紋深度的增加,固有頻率呈現(xiàn)明顯的下降趨勢(shì),尤其是前幾階固有頻率受裂紋的影響程度較大。
3試驗(yàn)驗(yàn)證
3.1實(shí)測(cè)齒輪箱振動(dòng)信號(hào)
為了模仿齒根裂紋,用線切割機(jī)在齒根過(guò)渡圓角危截面處全齒寬上切割寬0.3mm,深度分別為2mm,3mm,4mm和5mm的裂紋。
有限元仿真的正常齒輪的第10階固有頻率為708.17Hz,由采樣定理,取采樣頻率為2048Hz就可以了,采樣點(diǎn)數(shù)取為2048,輸入軸齒輪齒數(shù)z1=20,輸出軸齒輪齒數(shù)z2=30,輸入軸的回轉(zhuǎn)頻率為ƒr1=18.55Hz,因此嚙合頻率ƒm=371Hz。圖4和圖5分別給出了正常齒輪和裂紋齒輪(裂紋深度為4mm)的振動(dòng)信號(hào)時(shí)域波形圖。
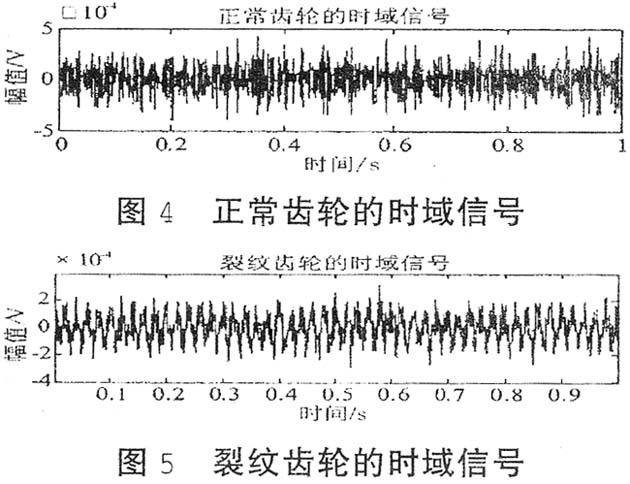
3.2模態(tài)參數(shù)的提取方法
通過(guò)前面的分析可以知道,齒輪發(fā)生裂紋故障時(shí),其模態(tài)參數(shù)(固有頻率)將會(huì)發(fā)生顯著的變化,因此可以考慮將固有頻率作為診斷齒輪裂紋故障的一個(gè)重要參數(shù)。
常用的模態(tài)分析方法有2種,即有限元理論分析法和試驗(yàn)?zāi)B(tài)分析法。
有限元理論分析法建立的結(jié)構(gòu)動(dòng)力學(xué)模型,不能足夠準(zhǔn)確的反映實(shí)際情況,因此計(jì)算的結(jié)果會(huì)有一定的偏差,但可將有限元計(jì)算結(jié)果作為試驗(yàn)分析的參考值,進(jìn)行信號(hào)的預(yù)處理。
傳統(tǒng)的試驗(yàn)?zāi)B(tài)分析法往往是通過(guò)測(cè)量工程結(jié)構(gòu)在非工作狀態(tài)下的激振力和響應(yīng),進(jìn)而采用頻響函數(shù)和脈沖響應(yīng)函數(shù)來(lái)識(shí)別模態(tài)參數(shù)。但是對(duì)于像齒輪箱這樣復(fù)雜的機(jī)械系統(tǒng),實(shí)現(xiàn)上述測(cè)量常常會(huì)面臨如下困難:激振力的測(cè)量難實(shí)現(xiàn);有些情況還不允許停機(jī)測(cè)試。本文提取模態(tài)參數(shù)的目的是為了將其用于故障識(shí)別,因此,需要尋找一種在線模態(tài)識(shí)別方法。
利用振動(dòng)信號(hào)直接進(jìn)行模態(tài)參數(shù)識(shí)別的常用方法有Ibrahim時(shí)域法、ITD法、最小二乘復(fù)指數(shù)法、多參考點(diǎn)復(fù)指數(shù)法、特征系統(tǒng)實(shí)現(xiàn)法和ARMA時(shí)序分析法。本文采用ARMA時(shí)序分析法對(duì)齒輪箱振動(dòng)信號(hào)進(jìn)分析,進(jìn)而提取系統(tǒng)的模態(tài)參數(shù)。在以往進(jìn)行頻域譜分時(shí),常由于信號(hào)截?cái)喽鹦孤,出現(xiàn)旁瓣、分辨率低及信號(hào)被淹沒(méi)等缺陷,而時(shí)間序列分析則與頻域譜分析不同,由于時(shí)序譜是動(dòng)態(tài)譜,觀測(cè)數(shù)據(jù)能外延,因此不會(huì)由于觀測(cè)數(shù)據(jù)的樣本長(zhǎng)度有限而產(chǎn)生上述缺陷。
3.3ARMA時(shí)序分析法原理
時(shí)間序列分析首先由觀測(cè)數(shù)據(jù)擬合一個(gè)時(shí)序模型,然后對(duì)該模型進(jìn)行分析研究,從而得出觀測(cè)數(shù)據(jù)的統(tǒng)計(jì)特性。由于實(shí)測(cè)時(shí)間序列反映了系統(tǒng)工作的動(dòng)態(tài)過(guò)程,因此蘊(yùn)含著系統(tǒng)的固有特性。建立時(shí)序參數(shù)模型的目的,就是把系統(tǒng)本身固有的特性很好地表達(dá)出來(lái)。
N個(gè)自由度的線性系統(tǒng)激勵(lì)與響應(yīng)之間的關(guān)系可用高階微分方程描述,在離散時(shí)間域內(nèi),該微分方程變成由一系列不同時(shí)刻的時(shí)間序列表示的差分方程,即ARMA時(shí)序模型方程:

式(1)表示響應(yīng)數(shù)據(jù)序列Xt與歷史值Xt-k,的關(guān)系,其中等式左邊為自回歸(AR)模型,右邊為滑動(dòng)均值(MA)模型,2N為自回歸和滑動(dòng)均值模型的階次,ak、bk分別表示待識(shí)別的自回歸系數(shù)和滑動(dòng)均值系數(shù),ft-k為白噪聲激勵(lì)。
運(yùn)用ARMA時(shí)序法識(shí)別模態(tài)參數(shù)首先要估算系數(shù)ak和bk的值,本文利用Prony方法對(duì)時(shí)間序列響應(yīng)進(jìn)行擬合獲得ARMA模型的參數(shù)(可以通過(guò)調(diào)用MATLAB中的prony函數(shù)實(shí)現(xiàn))。當(dāng)求得自回歸系數(shù)ak和滑動(dòng)均值系數(shù)bk后,通過(guò)ARMA模型傳遞函數(shù)的表達(dá)式計(jì)算系統(tǒng)的模態(tài)參數(shù),ARMA模型的傳遞函數(shù)為:

用代數(shù)方程求解法計(jì)算分母多項(xiàng)式方程的根:

求解得到的根為傳遞函數(shù)的極點(diǎn),他們與系統(tǒng)的模態(tài)頻率ωk和阻尼比的關(guān)系為:
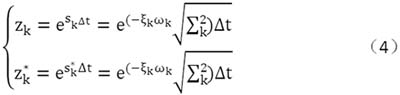
由式(4)可求得模態(tài)頻ωk和阻尼比,即:

3.4模態(tài)參數(shù)提取結(jié)果
本文首先用有限元法計(jì)算了試驗(yàn)齒輪的前10階固有頻率,并將其作為確定實(shí)際信號(hào)帶通濾波上下限的依據(jù),然后用ARMA時(shí)序分析法對(duì)濾波后的信號(hào)進(jìn)行處理,提取了不同裂紋深度的齒輪的前5階固有頻率值見(jiàn)表2。
表2 試驗(yàn)提取的固有頻率值 Hz
模態(tài) |
裂紋深度 |
2mm |
3mm |
4mm |
5mm |
1 |
259 |
257 |
255 |
241 |
2 |
303 |
300 |
295 |
290 |
3 |
367 |
360 |
359 |
352 |
4 |
454 |
452 |
444 |
434 |
5 |
531 |
530 |
524 |
524 |
從表2的模態(tài)參數(shù)識(shí)別結(jié)果來(lái)看,隨著裂紋深度的增加,提取到的固有頻率值也會(huì)有所降低,因此將固有頻率作為齒輪裂紋故障的診斷參數(shù)是可行的。
4結(jié)語(yǔ)
本文提出的方法避免了傳統(tǒng)方法診斷所帶來(lái)的不便之處,并且可以有效地診斷齒輪的齒根裂紋故障診斷中。對(duì)于其它類型的故障(如點(diǎn)蝕、磨損等)的診斷,本文也可以為其提供一個(gè)很好的參考思路和診斷方法。